This concept presents a highly efficient hydrogen storage and production system, designed to optimize performance and minimize long-term operational costs. At its core is a 10 kW PEM electrolyzer, seamlessly integrated with a photovoltaic (PV) system and supported by a high-capacity Redox Vanadium Flow (RVF) battery.
The configuration focuses on maximizing solar energy utilization through a consistent daily load profile, efficient hydrogen compression, and advanced storage techniques. It emphasizes hydrogen storage using Redox Flow batteries, offering a safer, longer-lasting, and more economical alternative to lithium batteries, especially for high-capacity applications.
Additionally, the system incorporates innovative hydrogen handling technologies—such as high-pressure PEM electrolyzers and cylinder-based storage solutions—ensuring flexibility for various use cases, including mobility, heating, and combined heat and power (CHP) systems.
By enabling self-sufficient hydrogen production and storage, this setup supports a scalable, future-ready hydrogen infrastructure, ideal for projects aiming to reduce grid dependence and maximize the return on hydrogen investments.
Contents
10 kW Electrolyzer with Hydrogen Storage and Redox Flow Battery. 1
Optimizing Photovoltaic Systems for Electrolysis and Hydrogen Storage. 1
Hydrogen Storage Technologies: Redox Flow vs Lithium Batteries 2
Innovative Hydrogen Storage Solutions: PEM Electrolyzers and Gas Compression Systems 3
Compressor for Hydrogen storage solution. 4
Hydrogen Storage Solutions: Cylinders for Efficient Storage and Utilization. 4
Maximizing Hydrogen Storage: Electrolysis and Power Conversion Efficiency. 4
Hydrogen Fuel Cell Vehicles: Cost-Effective Solutions for Stationary Use. 5
Hydrogen combined heat and power plant 5
Conclusion for best hydrogen storage solution. 6
Optimizing Photovoltaic Systems for Electrolysis and Hydrogen Storage
To maximize hydrogen production efficiency, the photovoltaic system configuration remains consistent on the best roof surfaces, ensuring optimal solar energy utilization.
The most effective roof areas for photovoltaic installation are south- and west-facing.
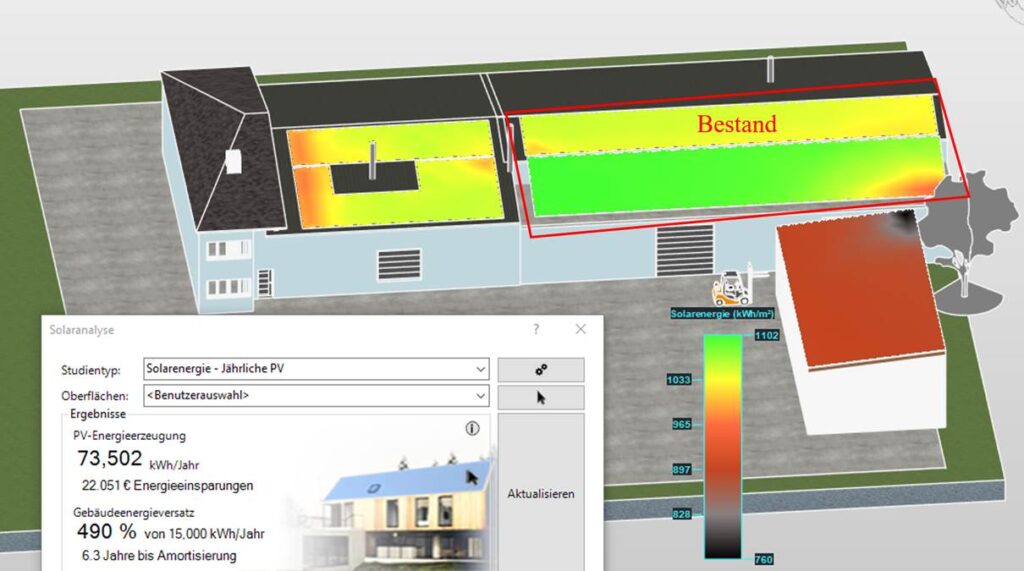
Illustration 1 Assumed roof areas for photovoltaics, 570 m² 80% occupied
Energy savings are based on the electricity not purchased at €0.30/kWh. However, electricity demand often does not align with solar supply.
For a 10 kW electrolyzer, the system follows a structured daily load profile. The electrolyzer operates at 1.8 Nm³/h, with excess hydrogen stored overnight in dedicated tanks or utilized through battery-powered electrolysis. Under a 5-bar pressure, the hydrogen night tank can hold 4.8 m³, while a larger tank at 30-bar pressure accommodates up to 144 Nm³.
Hydrogen compression aligns with peak solar availability, typically starting around noon when photovoltaic power is abundant. This ensures efficient energy distribution, allowing stored energy to be utilized effectively during morning hours.
To enhance storage reliability, a propane tank can be repurposed, provided it is verified to contain austenitic steel for material compatibility.
While the electrolyzer can operate at partial load, doing so impacts amortization rates and overall system efficiency. Therefore, maintaining high utilization is recommended to optimize return on investment.
The daily energy cycle mirrors previous analyses, with hydrogen production and compression regulated based on electrolysis capacity and compressor performance, ensuring continuous and efficient energy management.
Hydrogen Storage Technologies: Redox Flow vs Lithium Batteries
For this storage capacity, a Redox Vanadium Flow (RVF) battery is recommended. This liquid-based battery technology, manufactured in Germany, offers lower costs than lithium batteries for high-capacity storage.
Marketing information can be viewed at the following link.
https://voltstorage.com/technologie/die-flow-speichertechnologie
When comparing pump and stack costs, RVF batteries decrease in cost with larger tanks, while lithium batteries become more expensive due to their complex management systems. RVF batteries do not pose a fire risk and have a higher cycle life compared to lithium batteries, though their output power is lower.
Regarding life cycle costs, both RVF and lithium batteries cost approximately 10 cents per kilowatt-hour stored. When combined with the 6-cent production cost of PV electricity, self-stored electricity remains cheaper than purchasing from the grid.
Technical literature also recommends lower electricity costs for hydrogen production. A major disadvantage of lithium batteries is that they require replacements three times over the same cycle period, leading to increased costs and maintenance. In contrast, RVF battery service is available in Germany, whereas Chinese-manufactured lithium batteries may have limited support and accessibility.
For a 10 kW electrolyzer, Everflow Energy offers an RVF battery with a 120 kWh storage capacity of €103,000, which is well suited for the building’s 138 kWh daily electricity consumption.
Below is a life cycle cost comparison between lithium and RVF batteries.
Innovative Hydrogen Storage Solutions: PEM Electrolyzers and Gas Compression Systems
Batarow Hydrogen, based in Mecklenburg-Western Pomerania, manufactures PEM gas generators as part of their innovative approach to hydrogen storage solutions. Originally a sensor technology company, Batarow has expanded its offerings to include electrolyzers in recent years, providing a valuable addition to the hydrogen energy sector.
One of the key advantages of Batarow’s electrolyzers is their ability to operate at a pressure of 60 bar, simplifying the compression process and enhancing the efficiency of hydrogen storage. This feature makes them suitable for integration with hydrogen storage systems that require compressed hydrogen gas, improving the overall energy storage and distribution process.
Despite their potential, technical accessibility to Batarow’s electrolyzers can be challenging, as the company may be overwhelmed with inquiries, many of which may not be sufficiently qualified. However, with their continued innovation and focus on high-pressure electrolyzer technology, Batarow Hydrogen is contributing to the development of more efficient and sustainable hydrogen storage solutions.
Model | 10kW |
H2 Flow Rate (NL/hr)/(kg/100km) | 1808 |
Price € net | 51.995 € |
Price / Nl/hr €/W | €28.76 |
Compressor for Hydrogen storage solution
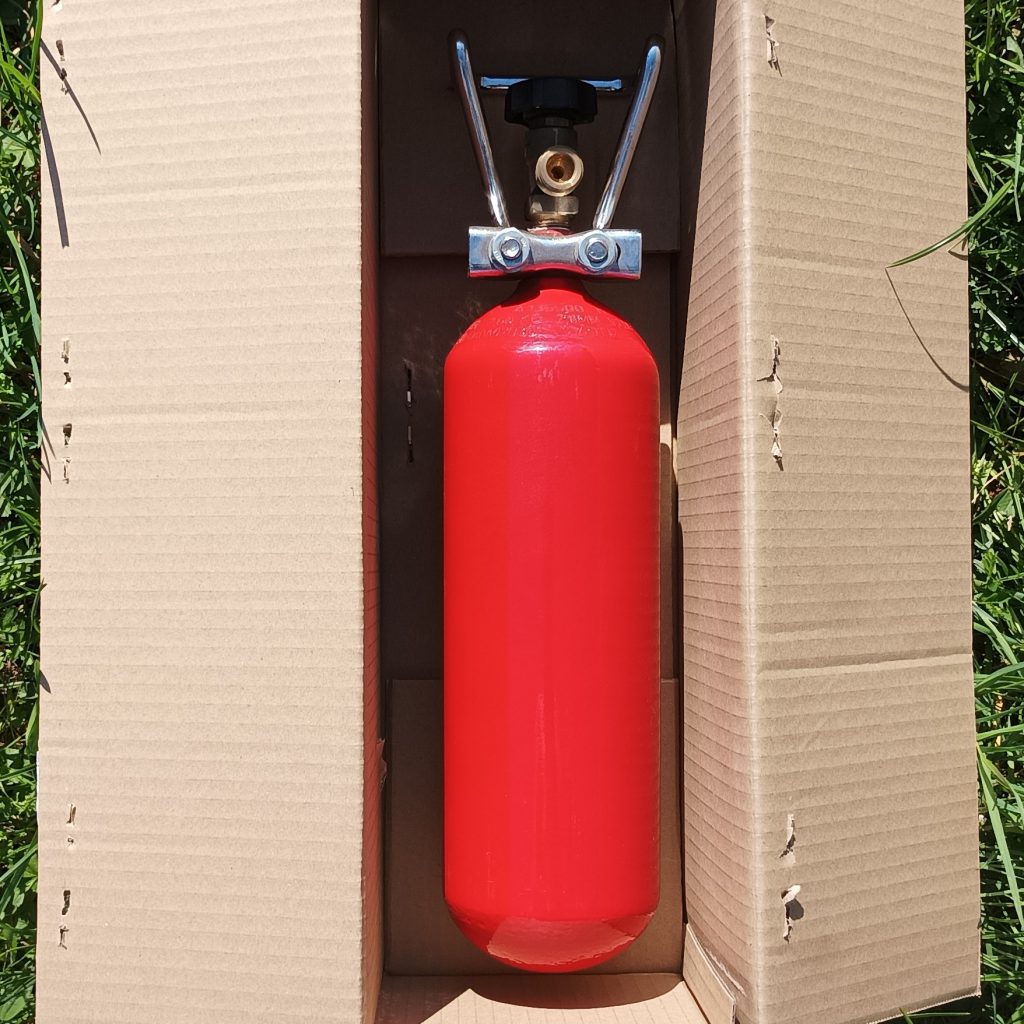
Sera, a German compressor manufacturer based in Hessen, produces a 2 m³/hr hydrogen compressor used in the PICEA hydrogen system. While the compressor offers reliable performance, a key concern is the cost and frequency of seal replacements, which the manufacturer has not yet specified. Understanding these maintenance aspects is crucial for long-term operational efficiency and cost management.
Model | pi-7007_02_de_agility_capability |
H2 Flow Rate (NL/hr)/(kg/100km) | 2000 |
Price € net | 26.000 € |
Price / Nl/hr €/W | 13,00 € |
Hydrogen Storage Solutions: Cylinders for Efficient Storage and Utilization
Nearly all year round, 43 Nm³ of hydrogen can be filled daily, equivalent to approximately 120 kWh of hydrogen or €20 worth of electricity per day. Every four days, a bundle of 12 bottles would be filled.
Each month, either 7.3 bundles of 12 bottles or 5.3 bundles of 16 bottles—costing €13,000—would be filled. To store hydrogen for six months, 30 bundles would be required.
For a 30% hydrogen admixture in the CHP plant, a supply of 5 Nm³ per hour would be necessary. An exchange-controlled feed-in could be an economical way to ensure year-round hydrogen utilization.
In 2024, electricity was purchased at over 30 c/kWh for 55 hours and at more than 25 c/kWh for 81 hours. A 15 kW CHP plant would not be profitable in such a short timeframe, making self-consumption the most viable option.
A 55-kW fuel cell vehicle offers greater potential for reconversion, as it can operate entirely on hydrogen.
Maximizing Hydrogen Storage: Electrolysis and Power Conversion Efficiency
If hydrogen is reconverted into electricity via a fuel cell with an efficiency of 50%, it aligns well with the company’s daily electricity requirements. Additionally, surplus hydrogen could be utilized in the mobility or heating sectors.
The estimated total cost for a 10 kW PEM electrolyzer, a 138 kWh RVF battery, a hydrogen compressor, low-pressure storage, and 30 hydrogen bundles is approximately €481,800.
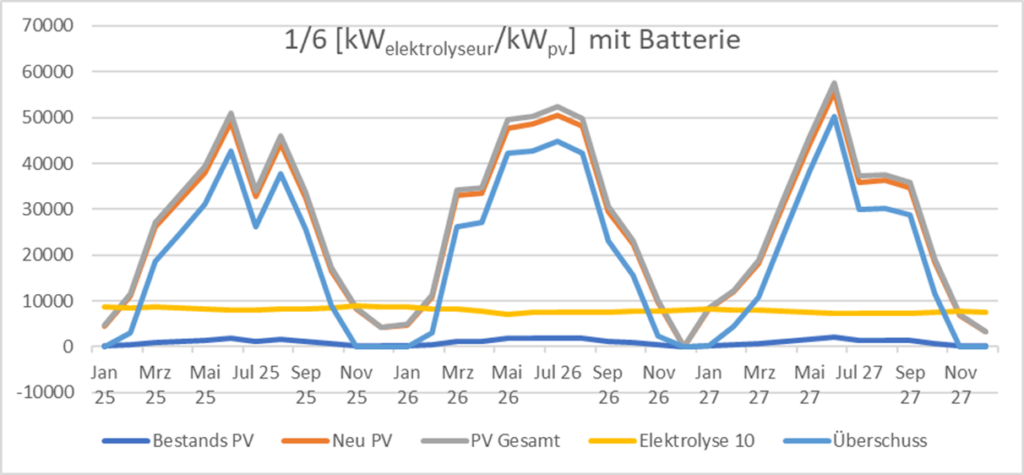
Illustration 2 Degree of utilization of photovoltaic electricity with 10 kW electrolysis for a 63-kW peak system
With one-sixth of the PV peak output, an electrolyzer in 24-hour operation reduces the surplus electricity more significantly. Only 1/3 of the PV electricity remains for feed-in or shutdown.
However, in a 1:6 power ratio, only 30% of the surplus electricity can be used for electrolysis. Consequently, 239,226 kWh would be fed into the public grid. Given a feed-in tariff of 7 cents per kilowatt-hour, this could generate annual revenue of €13,579, improving the overall amortization of the system.
By 2025, hydrogen will be traded in compressed gas cylinders at a minimum price of €4/kWh.
l | €/kg 2025 | €/kWh |
10 | 727 | 22,02 |
50 | 172 | 5,22 |
600 | 158 | 4,79 |
50 | 173 | 5,23 |
600 | 145 | 4,40 |
In addition to Gase Partner, hydrogen end customers such as Bayer in Wuppertal or Zinq in Westphalia can also be approached for hydrogen sales.
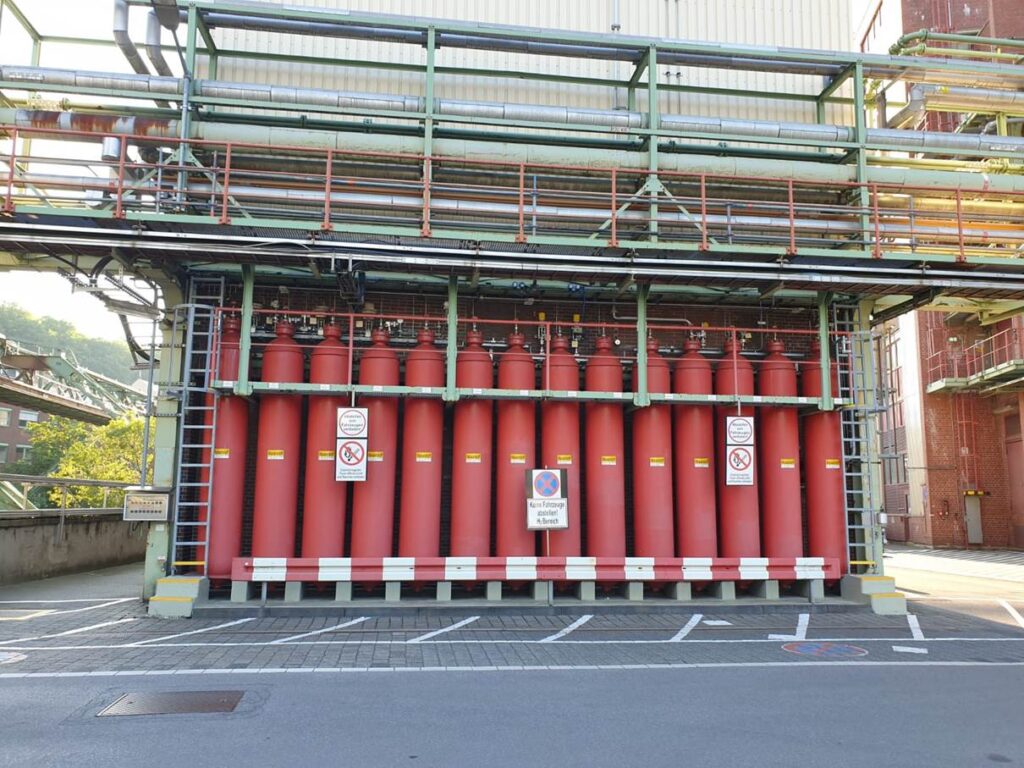
Illustration 3 Hydrogen storage Bayer Wuppertal
Illustration 4 https://www.zinq.com/aktuelles/2022/mit-wasserstoff-zur-gruenen-industriestadt/
Hydrogen Fuel Cell Vehicles: Cost-Effective Solutions for Stationary Use
The most affordable functioning hydrogen fuel cells on the market are found in Asian hydrogen vehicles, which are available second-hand. These vehicles can be repurposed for stationary applications with the expertise of skilled mechanics.
In 2025, a Toyota Mirai hydrogen vehicle, featuring a 55-kW fuel cell and having a mileage between 55,000 and 80,000 km (manufactured between 2019 and 2026), can be purchased for approximately €17,000.
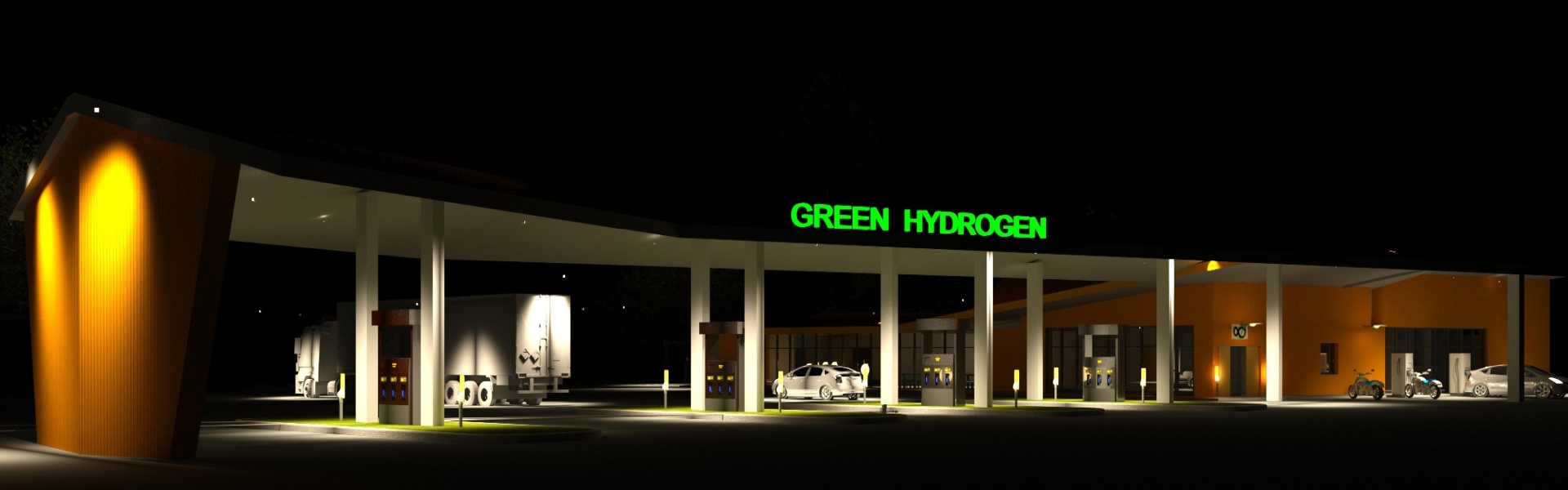
Hydrogen combined heat and power plant
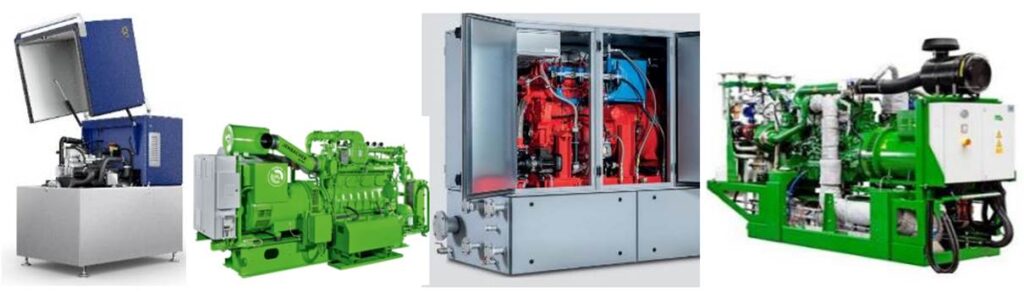
Figure 4 International electrolyzer price list v-electrolyzer.de
Hydrogen-combined heat and power plants are available from many German manufacturers. They can be used very dynamically. A market-driven, grid-serving feed-in into the grid is a common business model, with simultaneous use for local heating.
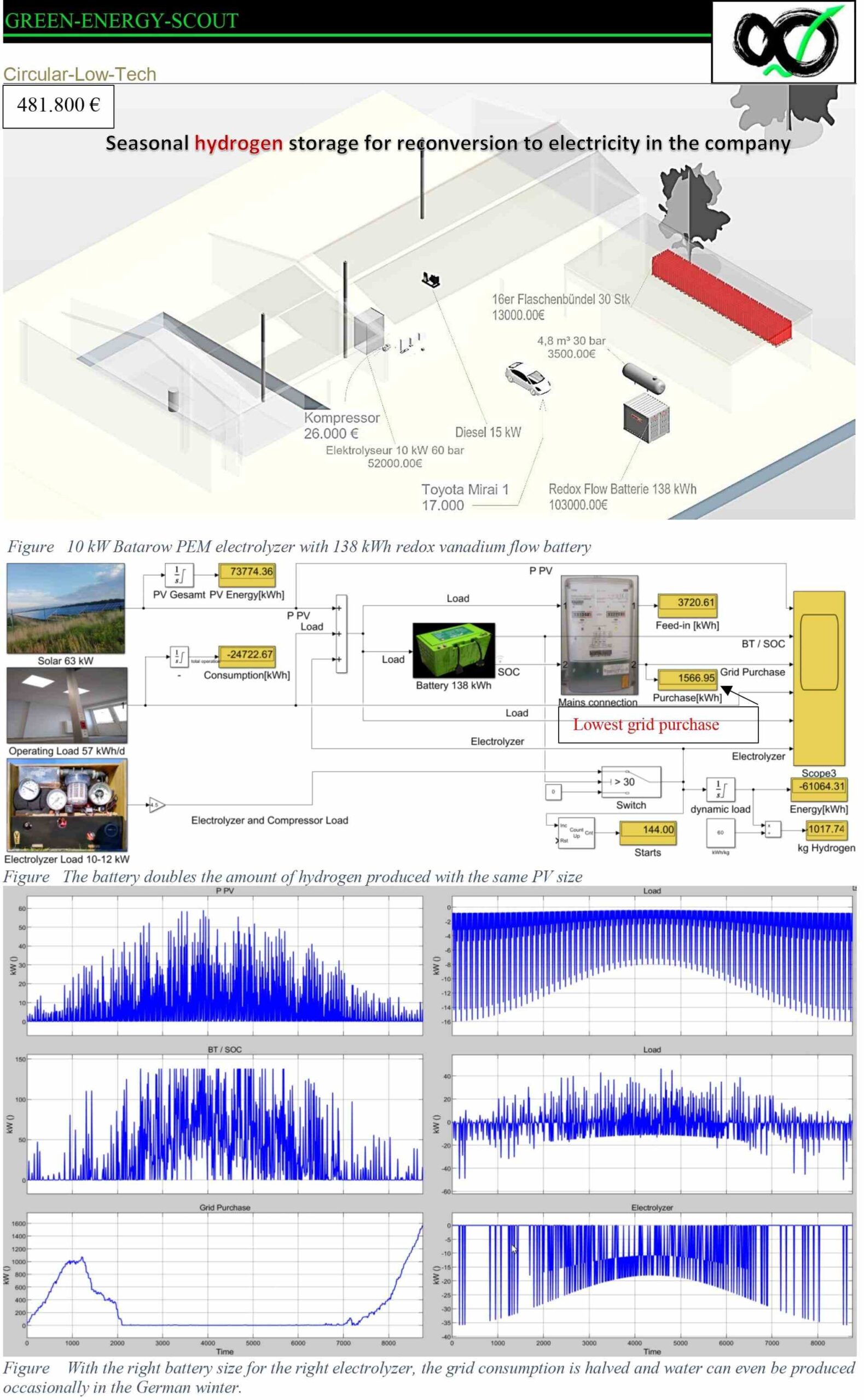
Conclusion for best hydrogen storage solution
The 10 kW PEM electrolyzer system, combined with Redox Vanadium Flow (RVF) battery storage and hydrogen compression technology, offers a highly efficient solution for sustainable energy production and storage. By integrating photovoltaic (PV) panels on south- and west-facing rooftops, the system maximizes solar energy utilization, generating excess electricity for hydrogen production during peak solar hours. The system’s design ensures optimal self-consumption of solar power, reducing grid dependence while offering the potential to sell excess energy back to the grid for additional income. The use of RVF batteries ensures long-term cost savings, offering a durable, fire-resistant alternative to lithium-ion batteries, with lower lifecycle costs.
Hydrogen storage is achieved through high-pressure cylinders and RVF batteries, providing a safe, scalable storage solution. Daily hydrogen production of 43 Nm³ is sufficient to meet energy needs for mobility, heating, and power generation. The integration of high-pressure PEM electrolyzers from Batarow, which operate at 60 bar, streamlines the compression process, enhancing efficiency. A hydrogen compressor from Sera ensures reliable storage and retrieval, though its long-term maintenance costs must be considered. The system’s flexibility allows for the efficient utilization of stored hydrogen in fuel cells or CHP systems, providing a versatile solution for both industrial and residential energy needs.
The overall system cost of approximately €481,800 covers all components, including the electrolyzer, storage systems, and hydrogen infrastructure. With annual grid feed-in revenue from surplus electricity estimated at €13,579, alongside income from hydrogen sales, the system offers a favorable return on investment. This setup supports a decentralized energy infrastructure and contributes to the development of green hydrogen economies, making it a cost-effective and future-ready solution for energy independence and sustainability.