Before investing in solar hydrogen, read this case study written by a leading low tech solar hydrogen engineering firm in Germany! Save capital by avoiding typical design flaws on solar hydrogen systems. Companies who want to reduce carbon emissions and invest in green hydrogen ask the following questions.
How much do different hydrogen systems cost for medium-sized companies?
How much hydrogen can be produced by solar on the companies’ roofs?
How much space do we need to add hydrogen to our solar system?
How much hydrogen needs to be stored?
How big does the electrolyzer for the ground-mounted PV or the PV system on the factory’s roofs need to be?
Does a battery make sense to increase electrolysis performance?
Which use of self-produced hydrogen makes the most sense, and which brings the highest profit?
How do I calculate the rough cost of a hydrogen project?
The attentive reader will get answers to these questions and many more in this brand-new hydrogen study on the cheapest hydrogen production with PV in the commercial sector by the solar hydrogen engineering firm green-energy-scout with branches in Berlin, Hamburg and Cologne.
The data for this study comes from the International Hydrogen Price List 2025.
1 In 2025 SMEs enlarge the solar system and resize energy storage
The existing photovoltaic system is to be expanded to reduce rising energy costs. The SME is considering equipping all available roof areas with photovoltaics as an off-grid system. Surplus electricity will be stored in the form of hydrogen. Various scenarios are proposed and priced for the use of hydrogen in this hydrogen study.
2 Summary of solar hydrogen engineering case study
4 variants of hydrogen production with suitably sized components were designed and priced. All prices are to be understood without delivery and installation. A budget of €100,000 was targeted by the client. A full-surface installation of photovoltaics on all roof areas does not make sense for electrolysis in the price range below half a million euros. A photovoltaic system without grid feed-in is less economical because, despite electrolysis, there is always surplus electricity for feed-in. With a little skill, a hydrogen system for a business can be purchased for just over €50,000. Surplus electrolysis allows the operator to experiment with converting combustion engines or repurposing used fuel cell vehicles.
Replacing the company’s internal propane gas forklift with a fuel cell forklift would only make sense in shift operation. The reconversion of hydrogen into electricity via a fuel cell is still not viable at current electricity prices. Even grid feed-in through a combined heat and power plant does not generate profit in lower power classes. The most economical use is the sale of hydrogen as a technical gas.
The shortest payback period is achieved with the largest electrolyzer (Variant 3: 90 kW, no battery) when a year-round buyer is secured. With 4,700 kg of hydrogen and a current hydrogen price of €16/kg at filling stations, a maximum revenue of €75,200 per year can be generated.
The combination of battery and medium-sized electrolyzer doubles the hydrogen production of the Variant 2: 10 kW Electrolyzer, Redox Flow Battery, the large amount of hydrogen to be stored for the company’s own needs increases the total price in such a way that only 10% savings are achieved with a quarter of hydrogen production compared to variant 3. The high electrolyzer costs in the small output range play their part in this.
The Enapter AEM electrolyzer has the worst amortization if it is operated as a short-term storage system without a large battery.
The last variant with the beginners electrolyzer has the lowest investment costs and is operated as an off-grid plant for hydrogen production. Year-round hydrogen use is also recommended for this variant. The maximum benefit lies in selling hydrogen as a technical gas. (Sold as technical gas)
3 Outlooks. In 2026 SMEs will optimize their solar hydrogen systems
As part of the further development of the dynamic calculation program for hydrogen systems, we will conduct more calculations in the future on the temporal filling level of the low-pressure storage tank, the compression process, its cycle count and operating hours, as well as the precise hydrogen storage capacity required for different hydrogen consumers.
Contents
1 In 2025 SMEs enlarge the solar system and resize energy storage. 1
2 Summary of solar hydrogen engineering case study. 1
3 Outlooks. In 2026 SMEs will optimize their solar hydrogen systems. 2
4 Solar hydrogen area potential for photovoltaics. 3
5 Funding for solar hydrogen investments. 3
6 Variants: Solar Hydrogen production. 3
6.1 Solar hydrogen engineering: 2.4 kW Elektrolyzer, Lithium Battery. 3
6.2 Solar hydrogen engineering: 10 kW Elektrolyzer, Redox Flow Battery. 7
6.3 Variant 3: 90 kW electrolyzer, no battery. 10
6.4 Equity variant. 1-3 kW most affordable hydrogen system for beginners. 11
7 Variants: Hydrogen appliances for businesses. 12
7.1 solar Hydrogen can be sold as technical gas. 12
7.2 Fuel Cell Vehicle for companies’ fleets. 13
7.3 solar hydrogen forklift 13
7.4 Hydrogen combined heat and power plant 14
8 Variant evaluation after dynamic simulation of 4 hydrogen plants. 14
4 Solar hydrogen area potential for photovoltaics
First, potential PV areas for converting radiant energy are evaluated.
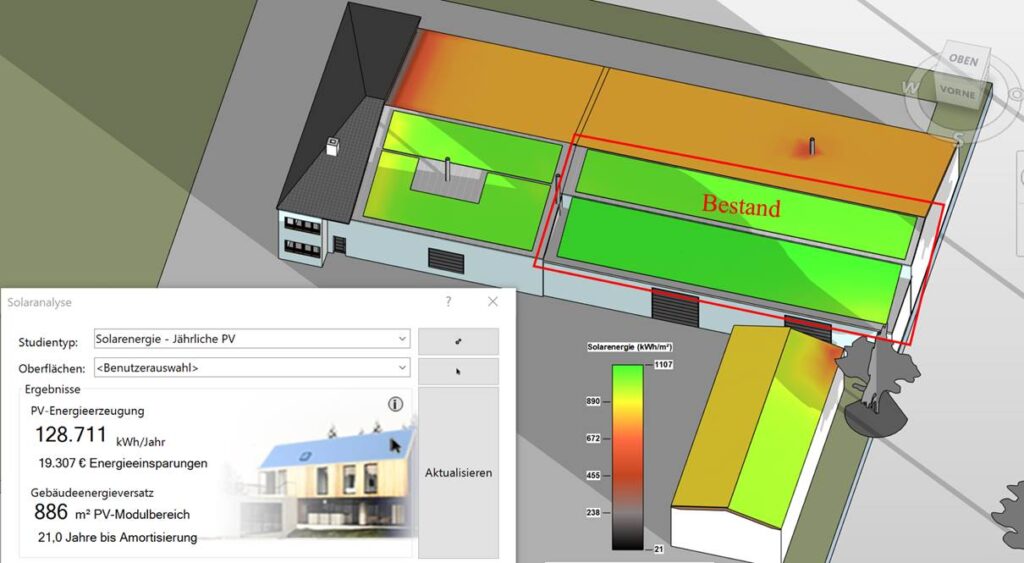
Illustration 2 Photovoltaics potential on the roof surfaces
Different strategies for cost-optimized hydrogen production are used in the variants.
5 Funding for solar hydrogen investments
The funding landscape remains somewhat limited due to the weak economy in 2025. However, KfW offers low-interest loans.
Credit No.270 – Renewable Energy Standard
A promotional loan for electricity and hydrogen electrolysis
- The most important facts in brief
- Loan starting from 4.53% APR
- Applicable for power and heat generation plants, grids, and storage facilities
- Supports photovoltaics, hydropower, wind, biogas, hydrogen, and more
- Available to private individuals, companies, and public institutions
6 Variants: Solar Hydrogen production
Three design variants for the electrolyzer have been chosen:
- Design with low investment costs and small space requirements for H2 storage systems
- Design with high investment costs but relatively inexpensive components
- The design focuses on excess minimization with minimal battery
Three of the best and most cost-effective gas generator companies in Europe are selected. A gas generator includes not only the electrolyzer but also control systems, water treatment, and gas drying.
All prices are non-binding, net, and based on 2023 data. The costs for PV systems, inverters, and other related components are not included in the hydrogen production cost estimates.
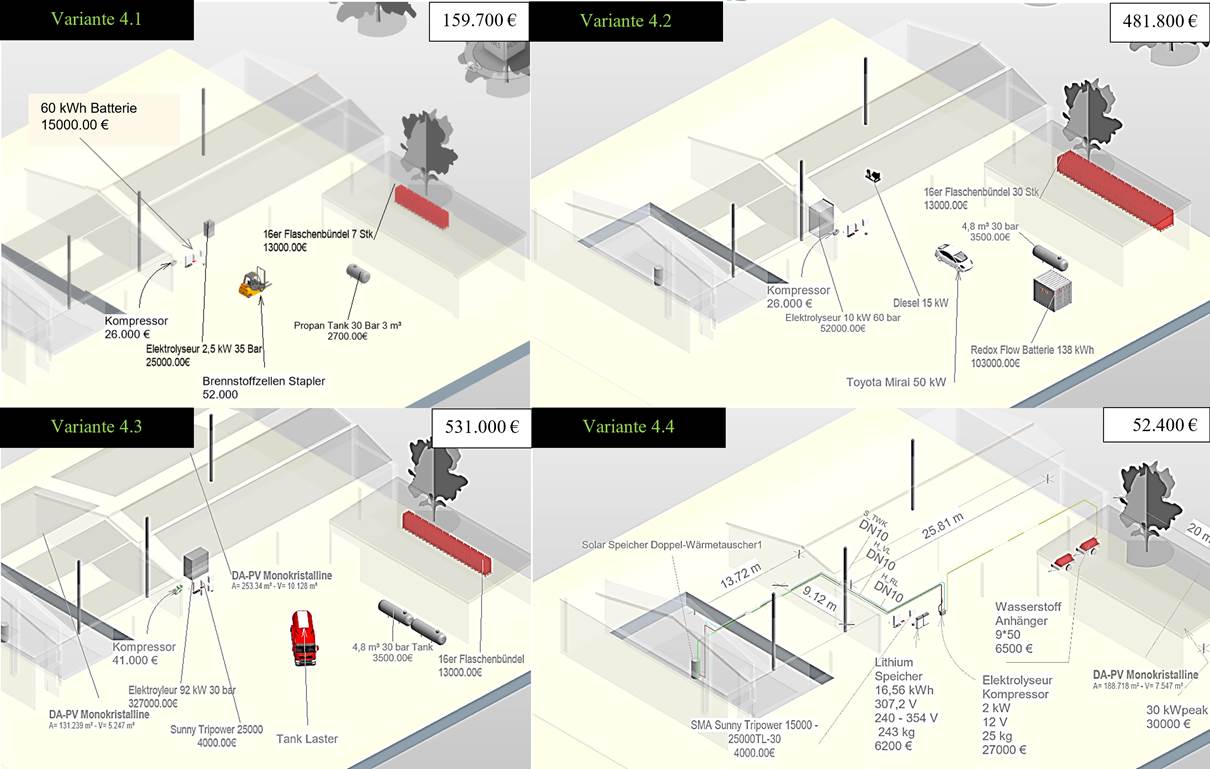
Illustration solar hydrogen engineering for SMEs, Price and h2 systems design overview
6.1 Solar hydrogen engineering: 2.4 kW Elektrolyzer, Lithium Battery
In this variant, the best roof areas for photovoltaics are fully utilized
6.1.1 Photovoltaics for green hydrogen
The south- and west-facing roof areas are the most effective.
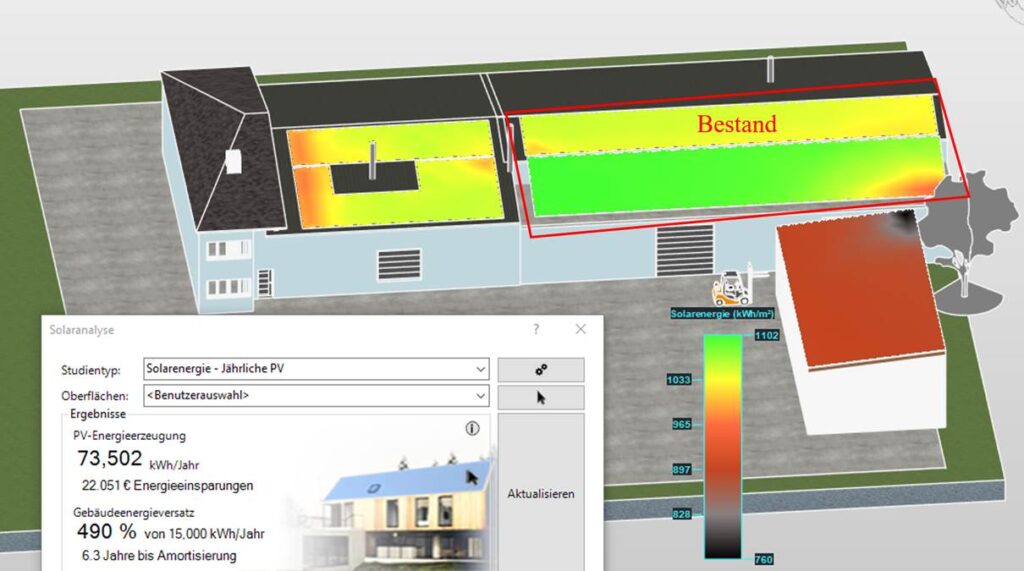
Illustration 3 Assumed roof areas for photovoltaics, 570 m² 80% occupied
The energy savings are based on electricity not purchased at 30 c/kWh. However, the electricity demand rarely matches the solar supply.
The following graph shows the electricity production from the existing PV system and the newly developed photovoltaic areas for the years 2025 to 2027. With these insights, an electrolyzer and battery can be dimensioned to minimize PV surplus and optimize the utilization of high-priced hydrogen components.
A dynamic display of energy generation trends, highlighting seasonal variations.
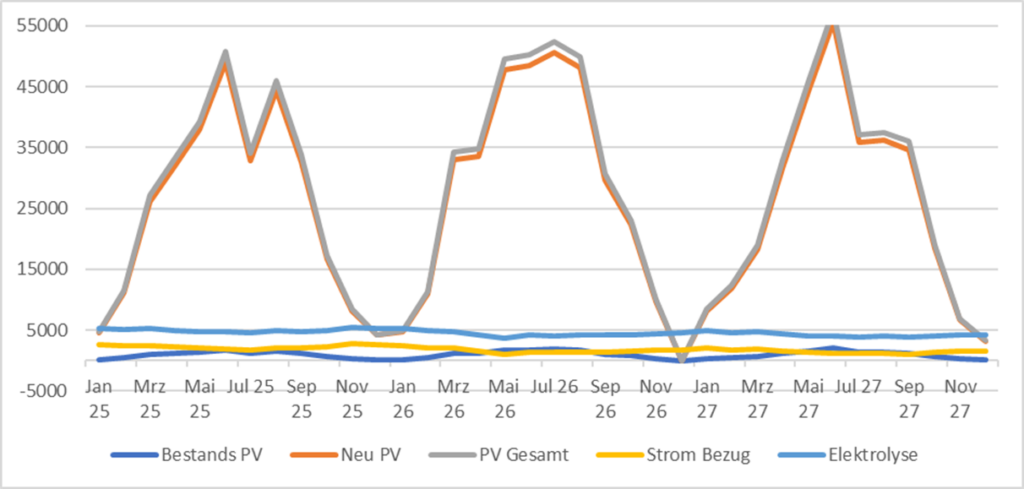
Illustration 4 Photovoltaics Forecast with Hydrogen Electrolysis in kWh. the grey graph is showing the solar production of which the electrolyzer uses a percentage in blue. The grid purchase is shown in yellow.
When examining specific days, the spring design is used randomly, as the prevailing low temperatures lead to the high efficiency of the PV modules, and the occasionally strong sun can cause power peaks in Germany.
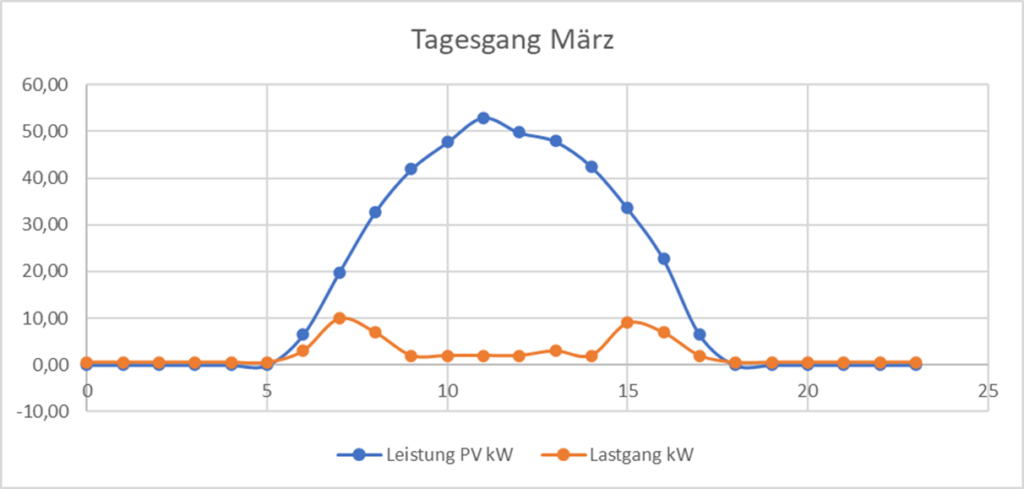
Illustration 5 Daytime Cycle PV Spring Peak Load Design
6.1.2 Battery storage for solar hydrogen engineering
A simple power balance between the electricity load of the user and the battery for electricity production from volatile renewables can serve as an initial approximation for battery sizing. The excess energy results from the load and the battery charge. The hydrogen compressor operates at 2.2 kW during the day, which increases the electrolyzer output. In the hydrogen industry, the term ‘standard cubic meters’ is used due to varying pressures. A standard cubic meter (Nm³) refers to gas at ambient pressure and 0°C. The compressor can compress 2 Nm³ of hydrogen per hour, while the Enapter electrolyzer produces 0.5 Nm³ of hydrogen per hour. Therefore, the compressor operates almost continuously every fourth hour of sunshine to compress the hydrogen produced during the night. The hydrogen storage tank must hold approximately 5 Nm³.
Hour of the day | Power PV kW of 67 kWpeak | Load profile kW | Electrolyzer | Battery |
1 | 0 | -0,5 | -3 | -3,5 |
3 | 0 | -0,5 | -3 | -3,5 |
5 | 0 | -0,5 | -3 | -3,5 |
7 | 6,49 | -3 | -3 | -1,51 |
9 | 32,73 | -7 | -5 | 20,73 |
11 | 47,68 | -2 | -5 | 40,68 |
13 | 49,8 | -2 | -5 | 42,8 |
15 | 42,52 | -2 | -5 | 35,52 |
17 | 22,74 | -7 | -5 | 10,74 |
19 | 0 | -0,5 | -3 | -3,5 |
21 | 0 | -0,5 | -3 | -3,5 |
23 | 0 | -0,5 | -3 | -3,5 |
Electricity kWh | -57 | Footprint | -43,51 | |
Excess kWh | 253,72 |
A Sungrow 40 kWh battery is traded for €13899. https://solarhandel24.de/products/sungrow-sbh400-batteriespeicher-40kwh
An alternative price for lithium batteries is assumed for an FM-Solar PV battery with 40 kWh capacity, priced at €8,896. https://www.fm-solar.de/batteriespeicher/batteriespeicher-pv-0-mwst/40-kwh-speicher-fm-solar-pv-akku-stapelbar-51-2v-200ah-lifepo4-lithium-0-privatpersonen_512402_14166/
A 60 kWh lithium battery is priced at €15,000.
6.1.3 Solar hydrogen Electrolyzer
Acta has been manufacturing alkaline electrolyzers to make solar hydrogen engineering for a very long time. Unlike PEM electrolyzers, potassium hydroxide is added to the water to make it electrically conductive. This reduces the need for precious metals in catalytic converters and improves service life. Additionally, the stacks are larger. Acta, which later became Enapter, has German-Italian origins but has unfortunately started working with China in 2023. Due to the company’s status as an AG, formalities have been introduced, and telephone availability now requires patience. While cooperation with China is beneficial for the company’s liquidity, it can negatively impact transport routes and working and environmental conditions during production. Apart from occasional software issues, no significant quality losses are reported. The Enapter electrolyzer will be offered without water treatment in 2025, which adds costs and necessitates research to determine the final price. The price from 2022 is referenced when the Enapter electrolyzer was still offered with water treatment.
Model | Electrolyzer (EL 2.1), Dryer, Watertank, Water purification, Connectors, KOH Kit, Rack, Without Gas Tank |
H2 Flow Rate(NL/hr)/(kg/100km) | 501 |
Price € net | 25.625 € |
Price / Nl/h €/W | 43,16 € |
In 2025, the EL 4.1 air-cooled electrolyzer will be available in a 35-bar version without water treatment for €17,745.00 net. This includes gas drying, a water tank, and some fittings.
6.1.4 Solar hydrogen Compressor
Sera is a German compressor manufacturer based in Hesse. The 2 m³/h hydrogen compressor is used in the PICEA hydrogen system. However, the issue lies with the seal replacements and their associated costs, which the manufacturer has not yet specified.
Model | pi-7007_02_de_agility_capability |
H2 Flow Rate(NL/hr)/(kg/100km) | 2000 |
Price € net | 26.000 € |
Price / Nl/h €/W | 13,00 € |
6.1.5 Solar hydrogen Cylinders for SMEs
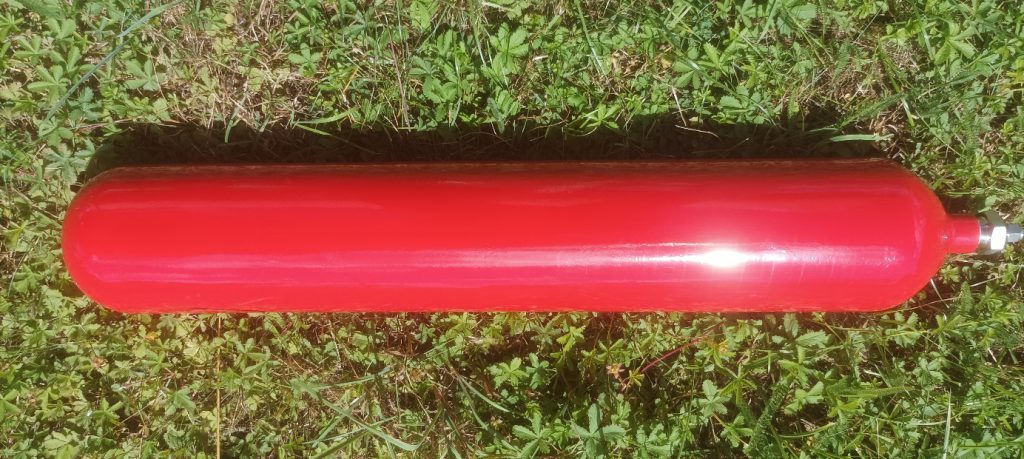
240 standard cubic meters of hydrogen can be stored in a 16×50-liter bundle. The electrolyzer needs to run for 480 hours to fill a bundle with 493 kWh. A target of 3,500 kWh for hydrogen production would require 7 bundles, resulting in an investment cost of €70,000. This would allow for year-round operation of a fuel cell forklift. Electrolysis occurs primarily during the summer months, while in winter, electricity is mainly used for direct consumption.
300 bar 1 mano 1 sectrion 1 ventil cylinders.cz | |
H2 Flow Rate(NL/hr)/(kg/100km) | 800 |
Price Neto | 12800 |
€/kWh | 34 |
6.1.6 Result: Simulink Hydrogen production model
A detailed look at PV system performance, highlighting surplus potential. Data-driven insights.
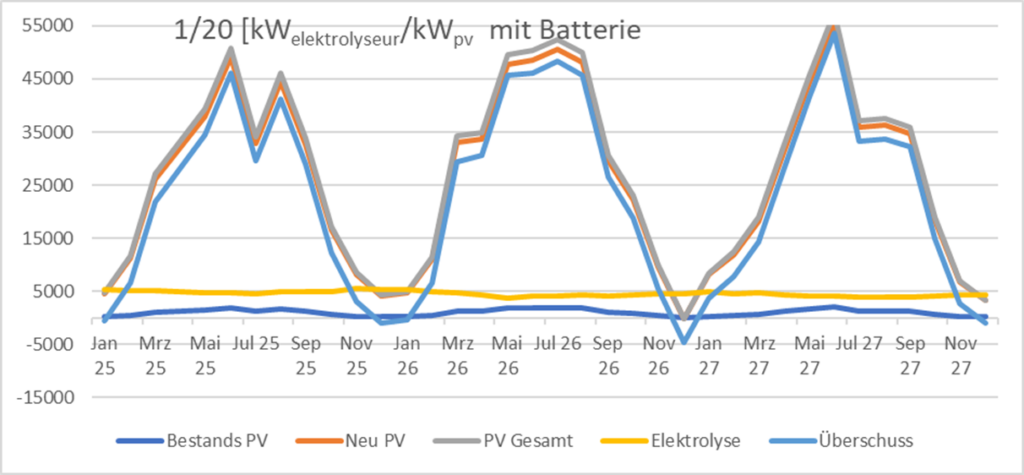
Illustration 6 Diagram of the PV surplus balance PV systems larger than 30 kW peak with low capital for electrolysis
The electrolysis system could run at full load for 10 months, which results in a high degree of utilization, positively affecting the amortization.
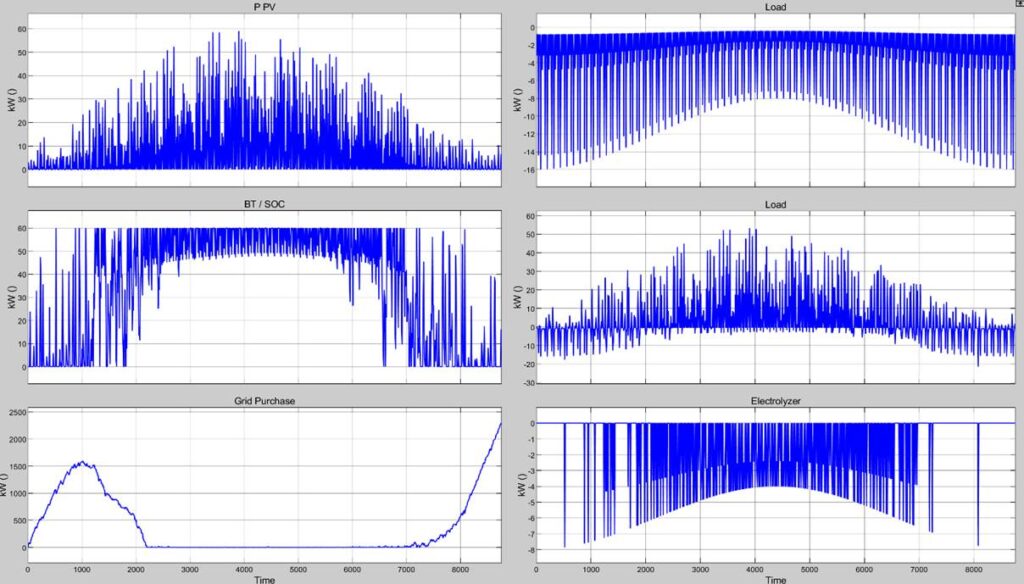
Figure 7 Electrolyzer or dynamic load simulation on an hourly basis
The graphs above show the switching cycle of electrolysis over the 8,760 hours of the year. The electrolyzer only operates when the battery is full, and solar power exceeds the electricity requirement. During winter, the electrolyzer requires slightly more power to heat the water. The graph at the bottom left shows that no hydrogen can be produced in winter. In the upper left, the photovoltaic output throughout the year is shown. The middle left displays the charge level of the battery over the year. The electricity purchase is shown at the bottom left. The middle right shows the load curve of the house with the electrolyzer, while the upper right illustrates the internal electricity use alone. The battery status is displayed in the middle left.
The hourly calculation of the power balance between electrolysis indicates that monthly balances are too imprecise to accurately determine electrolyzer utilization and the degree of photovoltaic system utilization.
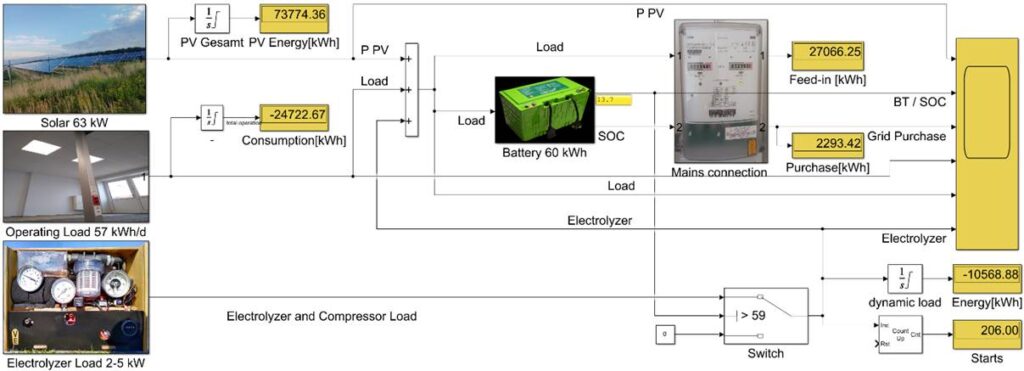
Figure 8: Solar energy flow chart of green hydrogen production
Using a 60 kW peak to produce hydrogen is a challenge for both the electrolysis capacity and gas bundle size. When combined with a lithium battery, a 2.5 kW electrolyzer can be operated with high efficiency. The electrolyzer only shuts down in December and January, leaving 490 kWh of hydrogen still available.
A major disadvantage is that, despite the battery and electrolysis, almost half of the converted PV electricity cannot be used. Direct marketing is recommended if purchases are made during peak times in the future.
The 2.5 kW AEM electrolyzer with a compressor, low-pressure gas tank, and 7,300 bar hydrogen cylinder bundles is estimated to cost €159,700. The use of hydrogen, such as for a hydrogen forklift, is not included in the estimated costs.
6.2 Solar hydrogen engineering: 10 kW Elektrolyzer, Redox Flow Battery
6.2.1 Photovoltaics size to make hydrogen
The photovoltaic system remains the same as in variant 6.1.
For a 10 kW electrolyzer, the daily load profile is as follows: The electrolyzer produces 1.8 Nm³/h. Overnight, 21 Nm³ of hydrogen can be stored temporarily while the battery can be used for electrolyzer operation. The hydrogen night tank will reach a capacity of approximately 4.8 m³ under 5 bar pressure, while a tank can hold 144 Nm³ at 30 bar.
The compressor starts up towards at noon for peak shaving, making the solar electricity available to users during the morning.
A propane tank is a good option for this. However, a check must be conducted to ensure that the steel is austenitic.
Of course, the electrolyzer can also run at partial load, but this will reduce the amortization rate.
The diurnal rate is similar to that in the previous chapter, based on the electrolysis capacity and compressor output.
6.2.2 Battery storage Redox Flow for solar hydrogen
For this storage capacity, a Redox Vanadium Flow (RVF) battery is recommended. This liquid-based battery technology is manufactured in Germany and offers lower costs than lithium batteries for high-capacity storage.
Marketing information can be viewed at the following link.
https://voltstorage.com/technologie/die-flow-speichertechnologie
While pump and stack costs decrease with larger RVF battery tanks, lithium batteries become more expensive due to their complex management systems. Additionally, RVF batteries do not pose a fire risk and have a higher cycle life compared to lithium batteries. However, their output power is lower.
When comparing life cycle costs, both RVF and lithium batteries cost approximately 10 cents per kilowatt-hour stored. When combined with the 6-cent production cost of PV electricity, self-stored electricity remains cheaper than purchasing from the grid.
Technical literature recommends lower electricity costs for hydrogen production.
A significant drawback of lithium batteries is that they require three replacements over the same cycle period, leading to additional costs and maintenance. In contrast, RVF battery service is available in Germany, whereas Chinese-manufactured lithium batteries may have limited support and accessibility.
For a 10 kW electrolyzer, Everflow Energy offers an RVF battery with a 120 kWh storage capacity of €103,000, which is well suited for the building’s 138 kWh daily electricity consumption.
The following is the life cycle cost comparison between lithium and RVF batteries.
6.2.3 the right Electrolyzer for solar hydrogen
PEM gas generators are also produced by Batarow Hydrogen, a company based in Mecklenburg-Western Pomerania. Originally a sensor technology company, Batarow has included electrolyzers in its portfolio for several years. However, technical accessibility is challenging, as the company is likely overwhelmed with unqualified inquiries. The electrolyzer pressure is rated at 60 bar, which simplifies the compression process.
Model | 10kW |
H2 Flow Rate (NL/hr)/(kg/100km) | 1808 |
Price € net | 51.995 € |
Price / Nl/h €/W | €28.76 |
6.2.4 solar hydrogen Compressor sizing
The compressor remains unchanged but operates for more hours compared to Variant 6.1
6.2.5 H2 Bundles, sizes and costs
Nearly all year round, 43 Nm³ of hydrogen can be filled daily, equivalent to approximately 120 kWh of hydrogen or €20 worth of electricity per day. Every four days, a bundle of 12 bottles would be completely filled.
Each month, either 7.3 bundles of 12 bottles or 5.3 bundles of 16 bottles—costing €13,000—would be filled. To store hydrogen for six months, 30 bundles would be required
For a 30% hydrogen admixture in the CHP plant, a supply of 5 Nm³ per hour would be necessary. An exchange-controlled feed-in could be an economical way to ensure year-round hydrogen utilization.
In 2024, electricity was purchased at over 30 c/kWh for 55 hours and at more than 25 c/kWh for 81 hours. A 15 kW CHP plant would not be profitable in such a short timeframe, making self-consumption the most viable option.
A 55 kW fuel cell vehicle offers more potential for reconversion. It can also be powered by 100% hydrogen.
6.2.6 Result of solar hydrogen engineering
If the hydrogen is reconverted into electricity via a fuel cell with an efficiency of 50%, it aligns well with the company’s daily electricity requirements. Additionally, surplus hydrogen could be utilized in the mobility or heating sectors.
The estimated total cost for a 10 kW PEM electrolyzer, a 138 kWh RVF battery, a hydrogen compressor, low-pressure storage, and 30 hydrogen bundles is approximately €481,800.
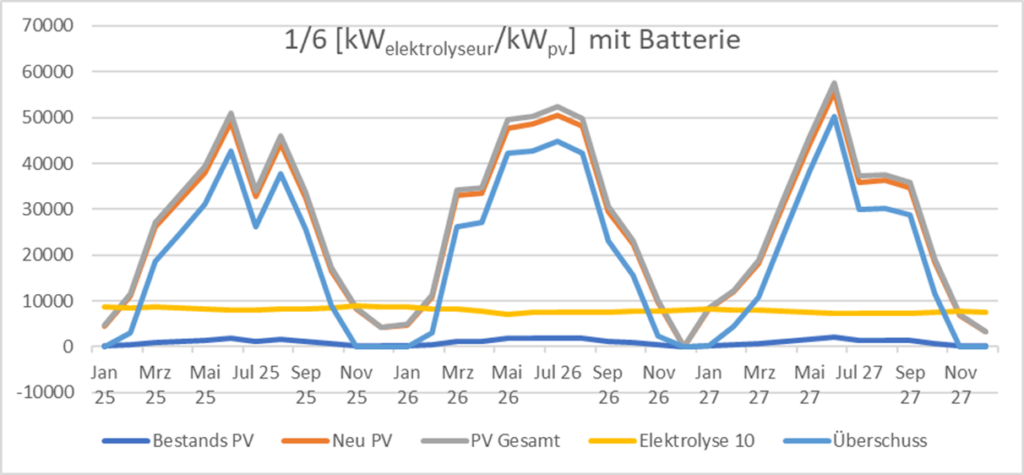
Illustration 1 Degree of utilization of photovoltaic electricity with 10 kW electrolysis for a 63 kW peak system
With an electrolyzer operating continuously at one-sixth of the PV system’s peak output, surplus electricity is significantly reduced. As a result, only one-third of the PV-generated electricity remains for feed-in or curtailment.
However, in a 1:6 power ratio, only 30% of the surplus electricity can be used for electrolysis. Consequently, 239,226 kWh would be fed into the public grid. Given a feed-in tariff of 7 cents per kilowatt-hour, this could generate annual revenue of €13,579, improving the system’s overall amortization.
6.3 Variant 3: 90 kW electrolyzer, no battery
In this variant, all available solar potential is utilized. The battery is dedicated solely to meeting the industry’s electricity needs and is not used for hydrogen production.
Erreduegas, an Italian company with 20 years of experience in manufacturing technical gas generators for industrial applications, specializes in compact and durable PEM electrolyzers. The company offers online diagnostics via a web interface and can be reached by phone. However, maintenance contracts outside Italy are not cost-effective.
For large electrolyzers, Erreduegas provides a highly competitive price of €16.5 per standard liter, making it one of the most affordable options in Europe.
6.3.1 PV array for green hydrogen production
Illustration 2: The photovoltaic potential of the roof surfaces can be fully utilized in this variant. The peak power is less critical, as it rarely reaches maximum levels on north-facing roofs. Even with elevated photovoltaic modules, self-shading is likely to occur, impacting overall efficiency.
6.3.2 Is battery storage necessary for green hydrogen facilities
The industry’s average daily electricity demand is 57 kWh.
A 60 kWh lithium storage system should be a good choice; however, it is not included in the cost calculations here.
6.3.3 Electrolyzer for SMEs with excess electricity
This seems to be the best 100 kW Electrolyzer for SMEs in Europe with less than 200 kW PV.
Model | Sirio 2000 |
H2 Flow Rate(NL/hr)/(kg/100km) | 20000 |
Price € net | 324.900 € |
Price / Nl/h €/W | €16.5 |
The costs for external water treatment, amounting to €8,500, are included in the calculations.
6.3.4 Compressor for 100 kW Electrolyzer
The 4-cylinder compressor is oil-lubricated, meaning the compressed hydrogen is only suitable for combustion engines. Consultants primarily specialize in natural gas compressors, with limited information available on hydrogen-specific models. The low price and feasibility assessment were based on a phone call and may need to be reconfirmed for accuracy.
0,08988 | |
Model | V 215/300 NG4 |
H2 Flow Rate(NL/hr)/(kg/100km) | 21500 |
Price € net | 41.000 € |
Price / Nl/h €/W | 1,91 € |
6.3.5 Hydrogen storage for SME
On average, 20 Nm³ of hydrogen is produced daily over 8 hours, equating to 500 liters at 300 bar. This production corresponds to 25 bundles of 12 bottles each, priced at €10,000 per bundle, per month. If the gas is collected twice a month, approximately 12 bundles will be required.
6.3.6 Result of hydrogen engineering
This variant optimizes the use of photovoltaic surpluses, with a 1:2 ratio of PV peak power to electrolyzer power.
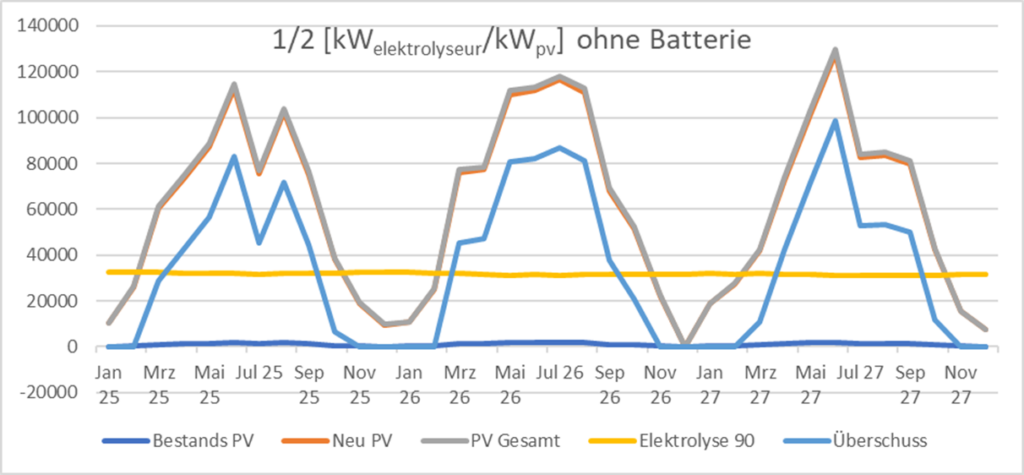
Illustration 2 Degree of utilization of photovoltaic electricity with 90 kW electrolysis and 180 kW peak power.
This variant only works if hydrogen can be sold to industry all year round or is dynamically used for electricity trading on the spot market all year round. The same approach can also be used with a smaller electrolyzer. However, the smaller electrolyzer then costs twice to three times as much per split hydrogen.
The 90 kW PEM electrolyzer with hydrogen compressor, low-pressure storage and 12 bundles is estimated at € 531,000. Almost 48% of the surplus electricity can be used. €23,062 feed-in tariff at 7 c/kWh can improve amortization.
6.4 Equity variant. 1-3 kW most affordable hydrogen system for beginners
After calculating various ratios between photovoltaic and electrolyzer power, with and without batteries, the variant with the lowest investment costs has now been calculated.
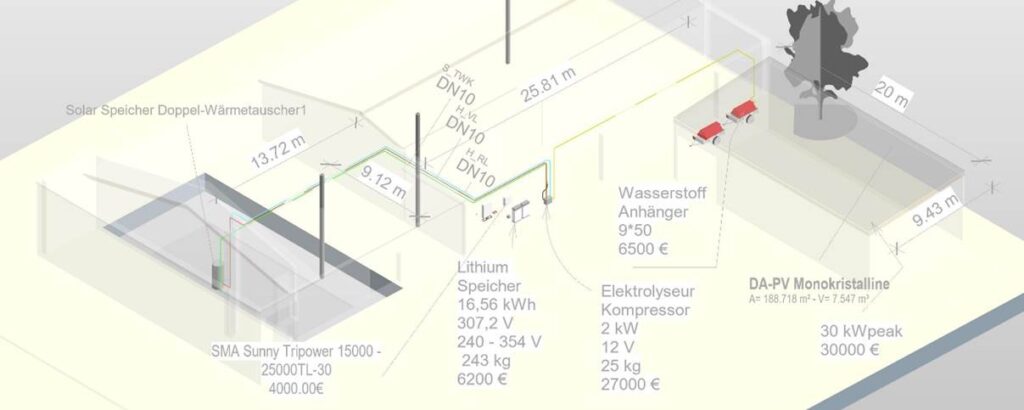
Illustration 3 The 1-3 kW electrolyzer utilizes the waste heat from the electrolysis process in the buffer storage tank, as shown by the green line
6.4.1 At which photovoltaic size hydrogen makes sense for SMEs
A 30 kW peak photovoltaic system is sufficient to enable hydrogen production.
6.4.2 Battery storage is mandatory for cost effective electrolyzers
The photovoltaic system is capable of charging two 15 kWh batteries and powering the electrolyzer directly during the day. At night, the batteries can supply power to the electrolyzer, enabling continuous operation over the weekends when the business is inactive.
6.4.3 Most affordable Electrolyzer
The electrolyzer has a nominal output of 830 watts. For an additional €5,000, a 3 kW PEM electrolyzer is also available. As can be seen, large-scale hydrogen production requires a significant number of steel cylinder bundles.
6.4.4 small hydrogen booster
The electrolyzer comes with an integrated 1 kW compressor that compresses the hydrogen to 300 bar during parallel operation.
6.4.5 Hydrogen tank as solar energy storage
In this case, hydrogen trailers are used as hydrogen storage systems, which enable easy transport of technical gas.
6.4.6 Solar hydrogen engineering Result
The variant with the small electrolyzer, paired with a suitable photovoltaic system and a medium-sized battery, offers the lowest risk for building the infrastructure of a hydrogen economy.
The estimated cost for the 1 kW PEM electrolyzer, hydrogen compressor, 32 kWh lithium battery, and 2 hydrogen trailers is €52,400.
7 Variants: Hydrogen appliances for businesses
This chapter describes various application scenarios for hydrogen from surplus electricity from a solar hydrogen engineering perspective. The different variants of hydrogen production can be combined with the desired hydrogen consumers.
7.1 solar Hydrogen can be sold as technical gas
Up to €3/kWh is paid for technical gases on the market. The hydrogen value chain should ideally be contractually agreed upon before the start of the project.
A significant portion of this €3/kWh end-customer value is allocated to the gas cylinder industry. This includes gas cylinder sales systems (renting, buying), transport, storage, and filling.
To determine the costs involved in marketing hydrogen in gas cylinders, I contacted Gase Partner in Witten. The following details emerged from a phone call.
Purchase Gas 16 bundle from Tyczka H2 3.0 300 bar
€ €/kg Kwh
400,0 25,03268 0,7585661
It follows that the gas wholesaler’s margin is four times the hydrogen value .
The following graph shows the consumer prices for hydrogen from 2021 to 2025 based on internal records.
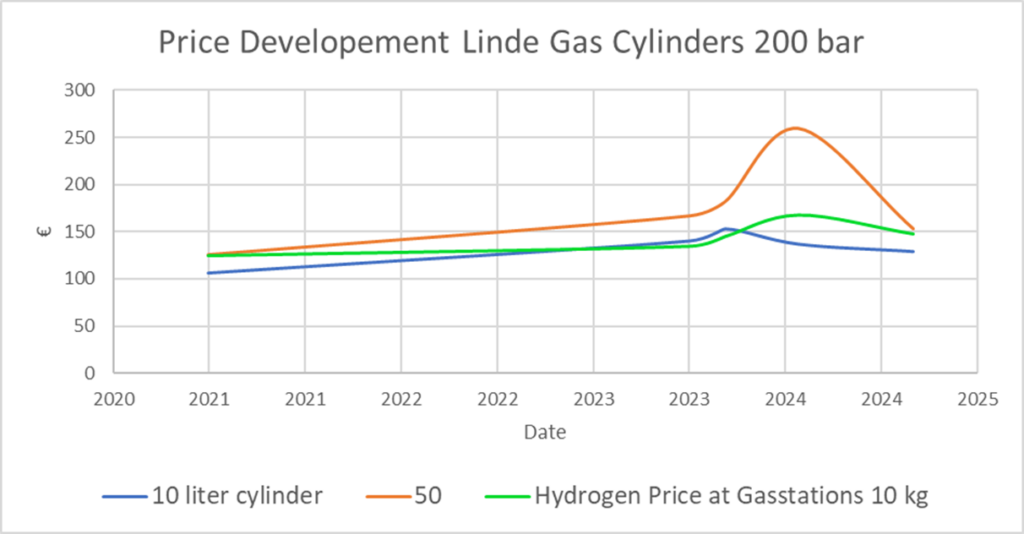
Illustration 9 Hydrogen Price Statistics for Technical Gas in Pressure Vessels
By 2025, hydrogen will be traded in compressed gas cylinders at a minimum price of €4/kWh.
l | €/kg 2025 | €/kWh |
10 | 727 | 22,02 |
50 | 172 | 5,22 |
600 | 158 | 4,79 |
50 | 173 | 5,23 |
600 | 145 | 4,40 |
In addition to Gase Partner, hydrogen end customers such as Bayer in Wuppertal or Zinq in Westphalia can also be approached for hydrogen sales.
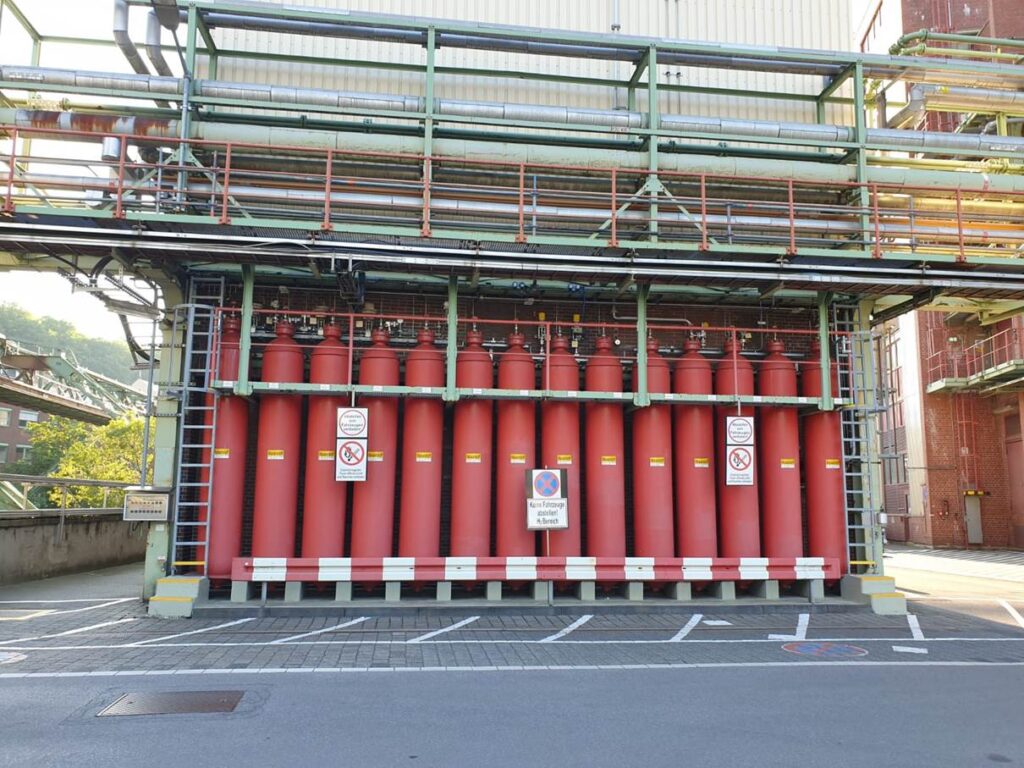
Illustration 10 hydrogen storage Bayer Wuppertal
Illustration 11 https://www.zinq.com/aktuelles/2022/mit-wasserstoff-zur-gruenen-industriestadt/
7.2 Fuel Cell Vehicle for companies’ fleets
The cheapest functioning fuel cells on the market are installed in hydrogen vehicles from Asia and can be purchased second-hand. For stationary use, the vehicles can be converted with skilled mechanics.
In 2025, a Toyota Mirai hydrogen vehicle with a 55 kW fuel cell, having 55,000–80,000 km mileage and built between 2019 and 2026, can be purchased for approximately €17,000.
7.3 solar hydrogen forklift
The existing gas forklift currently consumes an 11 kg propane gas cylinder per week at about €31. With a calorific value of 12.87 kWh/kg for piston engines, the energetic value of propane gas in cylinders is therefore 22 cents/kWh.
The existing Jungheinrich TFG 16 forklift truck (1991-1997) has an output of 39 kW.
The efficiency of a liquefied gas forklift is estimated at 35%.
A fuel cell industrial truck can achieve an efficiency of 45%. This means that only 127 kWh of hydrogen would be needed from the previous 141 kWh/week. Approx. 6,000 kWh are currently required for the gas forklift per year. In addition, there is no need to replace cylinders at the gas trader due to the self-produced electrolysis gas. In other words, the self-produced hydrogen would have an equivalent value of 24.2 cents/kWh.
The fuel cell forklift may need to be refueled every 6-8 hours. This shows that the strength of fuel cell forklifts only comes into its own in shift operation. At this logistics company, a battery forklift could be charged overnight and would last a shift.
It would be ideal if the forklift’s fuel cell provided the base load as electricity for the property overnight. Unfortunately, such bidirectional hydrogen systems are not provided by Plug Power.
7.4 Hydrogen combined heat and power plant
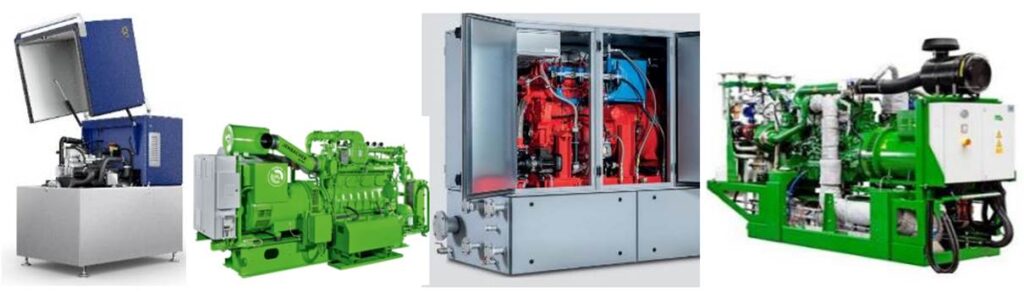
Figure 12 International electrolyzer price list https://v-electrolyzer.de
Hydrogen-combined heat and power plants are available from many German manufacturers. They can be used very dynamically. A market-driven, grid-serving feed-in into the grid is a common business model, with simultaneous use for local heating.
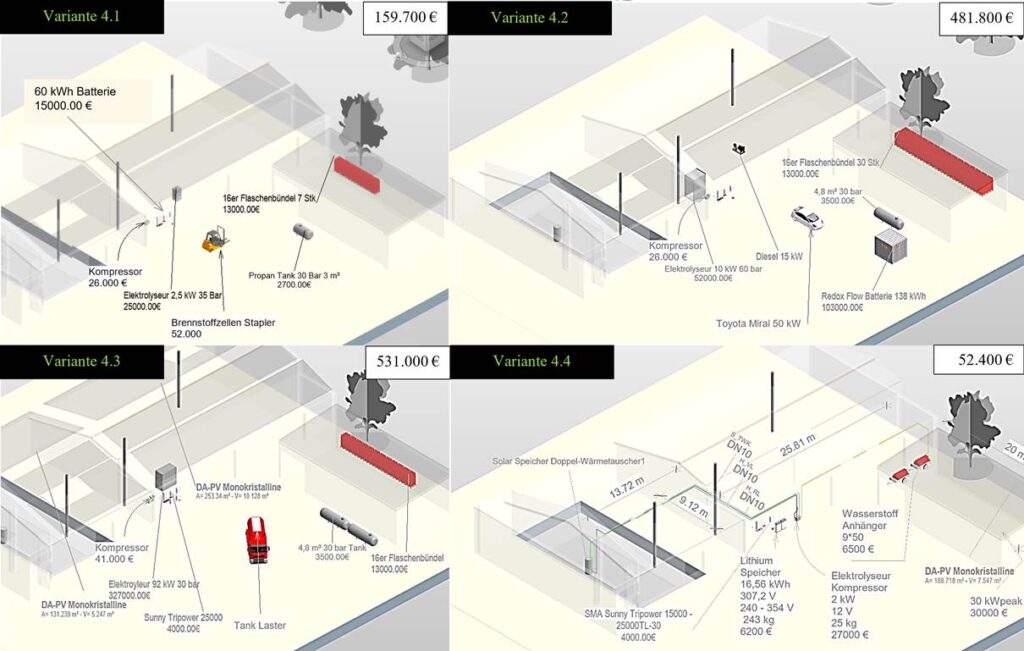
8 Variant evaluation after dynamic simulation of 4 hydrogen plants
Two basic principles of solar hydrogen engineering were applied and compared. In the first principle, the electrolyzer is operated every 24 hours. The low-cost batteries buffer renewable energy and allow small electrolyzers to reduce investment costs. Two different ratios of electrolyzer power to peak power with batteries were compared. In the case of the larger electrolyzer, the redox vanadium flow technology was used for reduced investment costs and longevity.
The second principle is a maximum PV system without a significant battery with a large PEM electrolyzer and piston compressor in volatile operation depending on the solar supply. The PV utilization rate is highest with this variant. However, the tanker truck should illustrate that such a large hydrogen production only works with regular hydrogen consumption.
The variety of storage systems for renewable energy and its smart adapted hydrogen components can achieve a high degree of self-sufficiency. Running costs for gas purchases, for example, are saved and added value in the form of hydrogen is stored timelessly.
Self-generated electricity can also provide sustainable mobility with an electric car or hydrogen vehicle.
The household electricity should be self-produced for consumption adapted to the sun. In addition, depending on the Variants: Hydrogen consumers safe from power outages.
Operating the PV system in island operation is not recommended for variants 1-3, as 5-digit revenues are to be expected even with low feed-in tariffs. For PV systems larger than 100 kW peak, the only option is direct marketing. The costs of stock market trading are high and reduce revenues.
Variant 4, consisting of a 30 kW peak PV system, a 32 kWh battery, and a 1-3 kW electrolyzer, seems to be the best variant to keep initial investment and infrastructure low. With the hydrogen produced, consumers can be tested, and trade relationships can be developed until scaling up to, for example, variant 4 is worthwhile because there is a buyer of hydrogen.
For all variants, approx. 50 m stainless steel cable with clamps are available for 500 €, fittings for 500 €, 10 m of cable of various cross-sections with accessories are 300 €, if necessary, hose and tank nozzle 6,500 € H2 or 1,000 € CNG, gas detector and safety technology 300 € and otherwise. At 1,000 €, i.e. min. €3,600 to €9,100 without delivery and installation.
Hydrogen pipes 6 mm can be accepted at 20 €/m. Fittings such as needle valves with 100 €/ piece and fittings such as elbows with 20 €/ piece can be summed up to determine the cost of hydrogen lines.
Prices for hydrogen pipelines with fittings up to 300 bar
Illustration 4 1 kW Beginners electrolyzer with 30 kWh battery and 2 hydrogen trailers
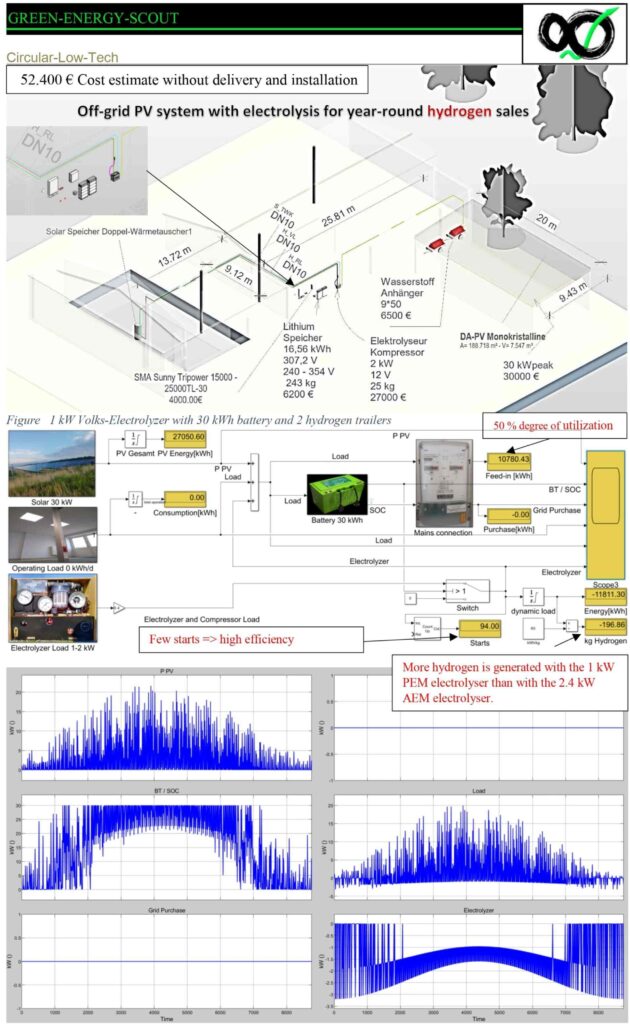
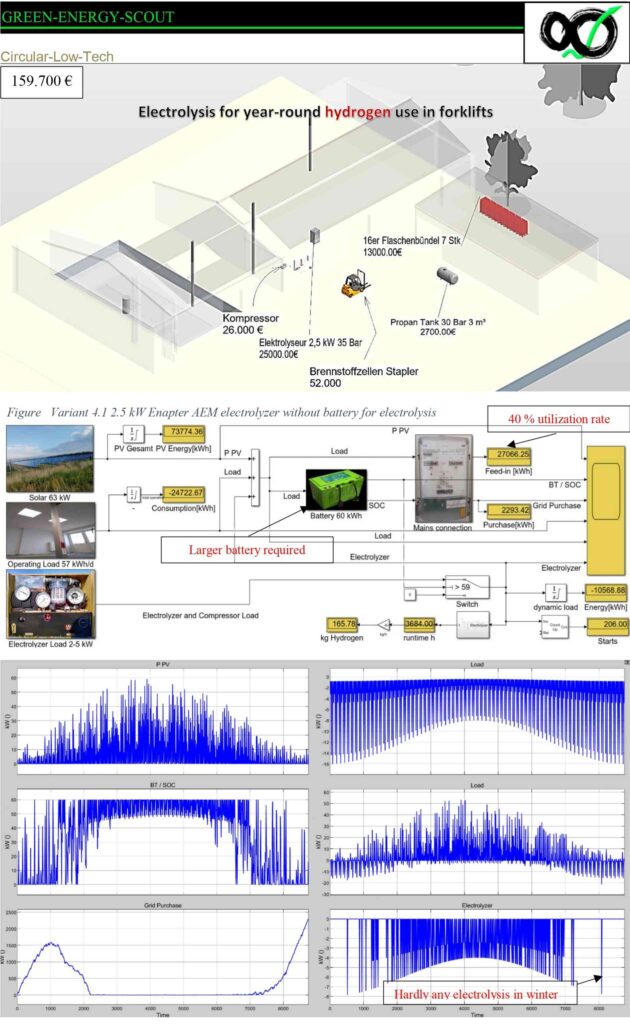
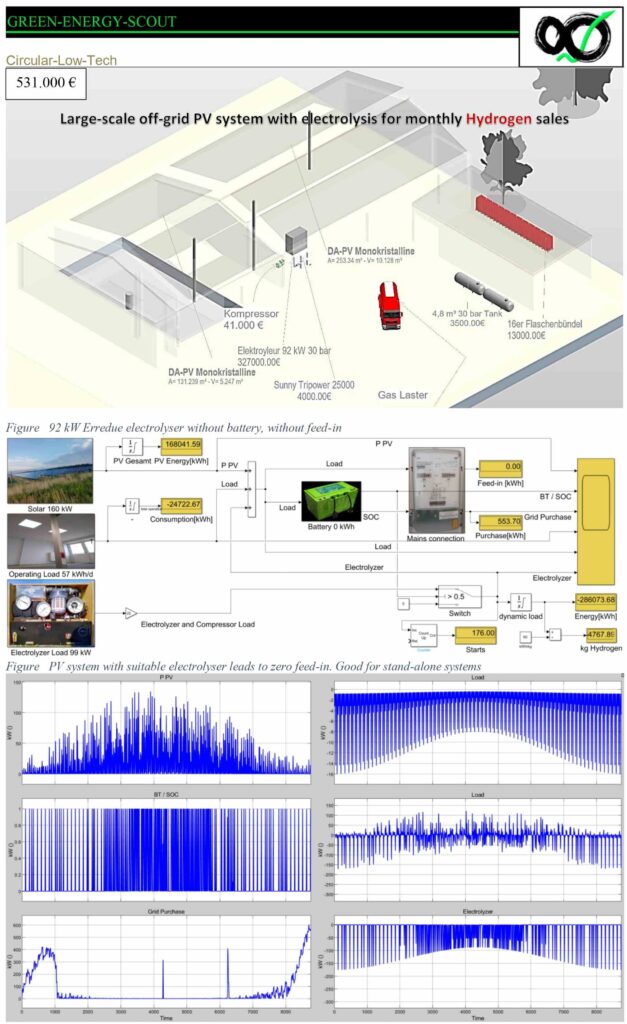
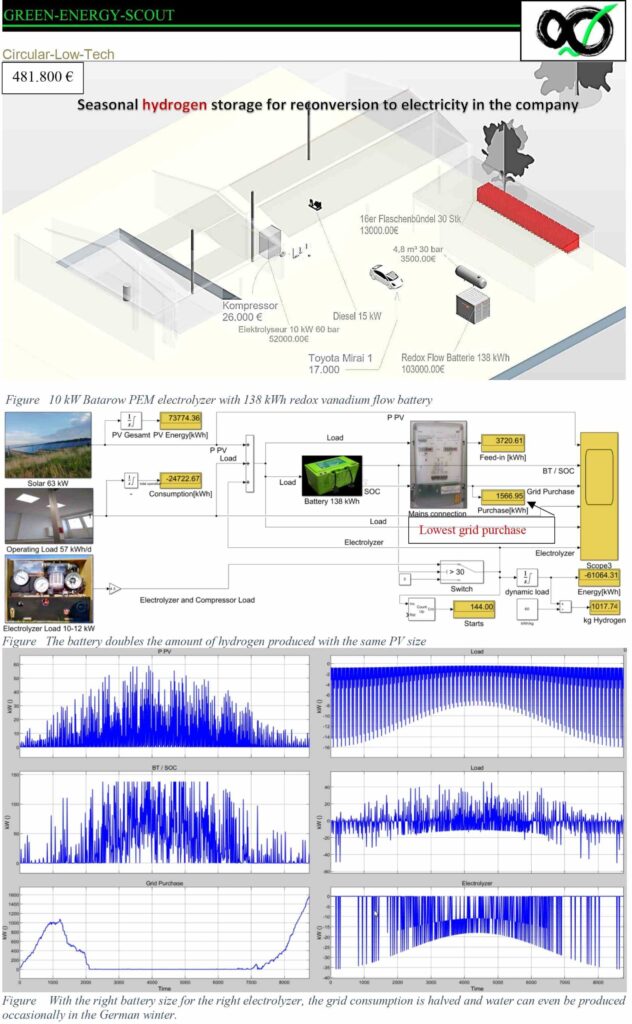
10 Disclaimer
The assumed values are very rough estimates based on the level of detail of the project. None of the estimated calculations should be used for the construction project and must be commissioned separately. The creator is not liable for any deviations.
All information has been conscientiously prepared according to recognized technical standards.
If you want your solar hydrogen engineering system to be simulated for your specific location, feel free to contact us.