The global shift toward renewable energy has underscored the need for integrated systems that combine efficiency, sustainability, and energy independence. This analysis focuses on optimizing hydrogen production using photovoltaic (PV) systems, supported by battery and hydrogen storage solutions. By aligning energy generation with demand through smart integration, the system ensures efficient use of solar power across daily and seasonal variations. Core technologies evaluated include electrolyzer types (PEM, alkaline, AEM), lithium-ion and vanadium flow batteries, hydrogen compressors, and various gas storage methods. Each component is assessed for performance, cost, and operational compatibility within a decentralized energy setup.
The study uses detailed PV forecasts, hourly load profiles, and hydrogen production simulations to determine the ideal system configuration for both residential and light industrial applications, such as fuel cell-powered forklifts. Seasonal analysis highlights the challenges of winter operation and surplus management during peak summer production. Although advanced battery storage and electrolyzers reduce energy waste, nearly 50% of PV electricity remains unused—indicating the need for direct marketing strategies. The findings emphasize the importance of system design in maximizing self-consumption, reducing reliance on the grid, and leveraging hydrogen as a clean energy carrier for year-round energy autonomy.
Contents
2.4 kW Electrolyzer with Hydrogen Production and Lithium Battery. 1
Hydrogen Production Optimization with Photovoltaic Systems 1
Battery Storage Solutions for Efficient Hydrogen Production. 1
Comparing Electrolyzer Technologies: Alkaline vs. PEM for Hydrogen Production. 2
Hydrogen Compressor Solutions: Performance and Maintenance Considerations 3
Industrial Hydrogen Cylinders: Storage Capacity and Investment For Hydrogen Production. 4
Results and Insights: Electrolyzer Utilization and Hydrogen Production Efficiency. 4
Hydrogen Forklifts: Efficient Energy Solutions for Industrial Applications 5
Conclusion for best Hydrogen Production Solutions 5
Hydrogen Production Optimization with Photovoltaic Systems
The most effective roof areas for photovoltaic installation are south- and west-facing.
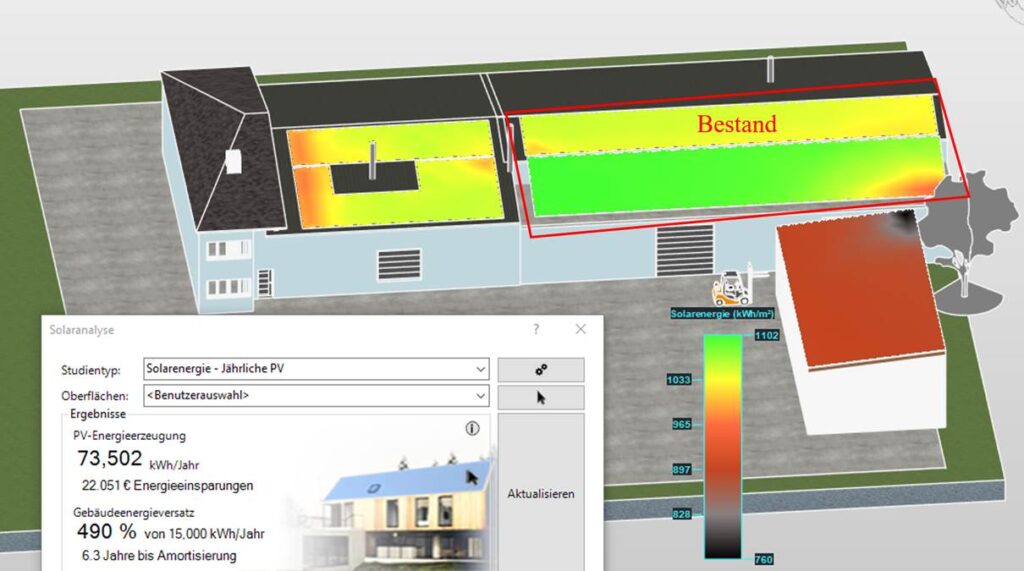
Illustration 1 Assumed roof areas for photovoltaics, 570 m² 80% occupied
Energy savings are based on the electricity not purchased at €0.30/kWh. However, electricity demand often does not align with solar supply.
The following graph shows the electricity production from the existing PV system and the newly developed photovoltaic areas for the years 2025 to 2027. With these insights, an electrolyzer and battery can be dimensioned to minimize PV surplus and optimize the utilization of high-priced hydrogen components.
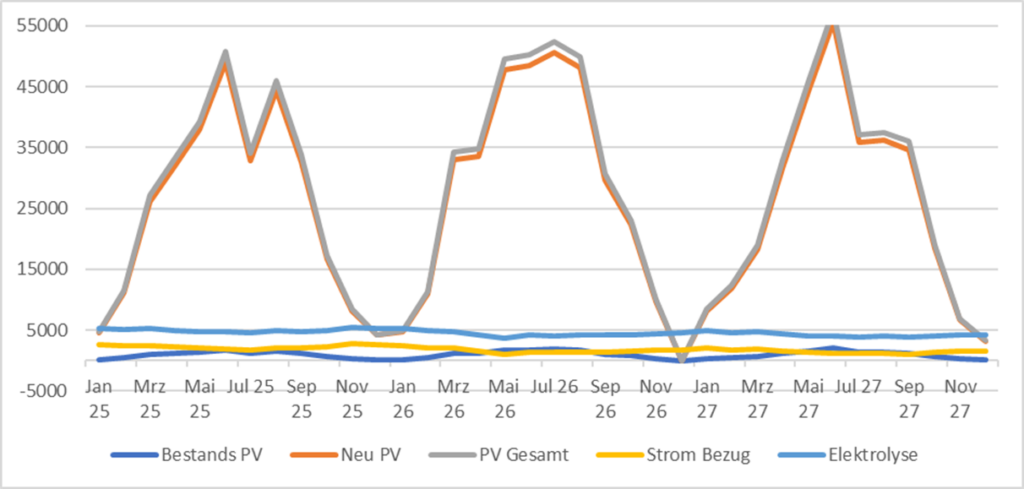
Illustration 2 Photovoltaics Forecast with Hydrogen Electrolysis in kWh
When analyzing specific days, the spring design is applied randomly, as the prevailing low temperatures enhance the efficiency of PV modules, while the occasional strong sunlight in Germany can cause power peaks.
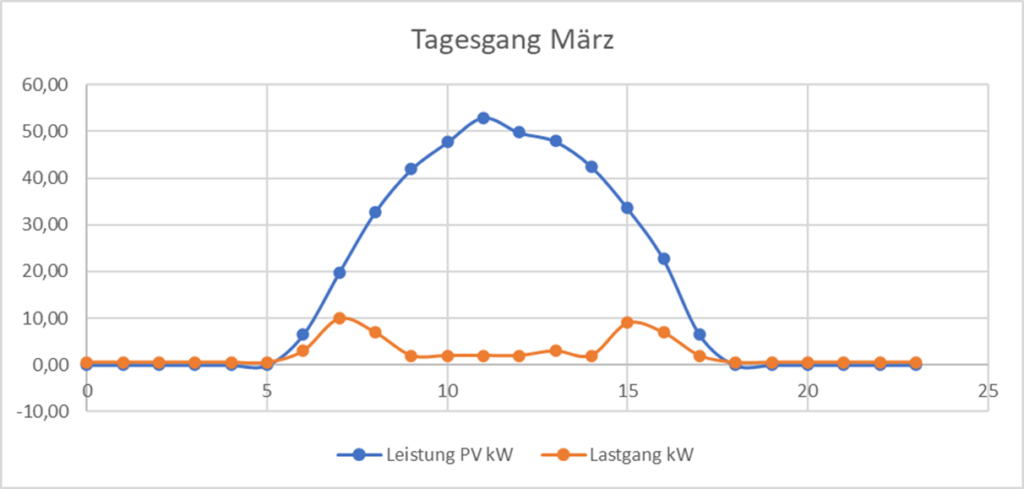
Illustration 3 Daytime Cycle PV Spring Peak Load Design
Battery Storage Solutions for Efficient Hydrogen Production
A well-balanced integration of battery storage with the user’s electricity load ensures efficient power generation from variable renewable sources. This approach provides an initial estimate for battery sizing by considering excess energy availability, battery charge levels, and user demand. During daylight hours, a hydrogen compressor operates at 2.2 kW, boosting electrolyzer efficiency. In hydrogen production, standard cubic meters (Nm³) is the preferred unit due to pressure variations, with 1 Nm³ representing gas at ambient pressure and 0°C. The compressor processes 2 Nm³ of hydrogen per hour, whereas the Enapter electrolyzer generates 0.5 Nm³ per hour. Consequently, the compressor runs almost continuously every fourth hour of sunshine to handle the hydrogen output accumulated overnight. To ensure a stable supply, the hydrogen storage tank must accommodate approximately 5 Nm³.
Hour of the day | Power PV kW of 67 kW peak | Load profile kW | Electrolyzer | Battery |
1 | 0 | -0,5 | -3 | -3,5 |
3 | 0 | -0,5 | -3 | -3,5 |
5 | 0 | -0,5 | -3 | -3,5 |
7 | 6,49 | -3 | -3 | -1,51 |
9 | 32,73 | -7 | -5 | 20,73 |
11 | 47,68 | -2 | -5 | 40,68 |
13 | 49,8 | -2 | -5 | 42,8 |
15 | 42,52 | -2 | -5 | 35,52 |
17 | 22,74 | -7 | -5 | 10,74 |
19 | 0 | -0,5 | -3 | -3,5 |
21 | 0 | -0,5 | -3 | -3,5 |
23 | 0 | -0,5 | -3 | -3,5 |
Strombedarf kWh | -57 | Footprint | -43,51 | |
Excess kWh | 253,72 |
The Sungrow 40 kWh battery comes at a price of €1389. https://solarhandel24.de/products/sungrow-sbh400-batteriespeicher-40kwh
As an alternative, the FM-Solar PV battery with 40 kWh capacity is available for €8896. https://www.fm-solar.de/batteriespeicher/batteriespeicher-pv-0-mwst/40-kwh-speicher-fm-solar-pv-akku-stapelbar-51-2v-200ah-lifepo4-lithium-0-privatpersonen_512402_14166/
For a higher capacity option, a 60-kWh lithium battery is priced at €15,000.
Comparing Electrolyzer Technologies: Alkaline vs. PEM for Hydrogen Production
Acta has a long history of manufacturing alkaline electrolyzers. Unlike PEM electrolyzers, alkaline electrolyzers use potassium hydroxide in water to enhance electrical conductivity. This reduces reliance on precious metal catalysts and extends service life. Additionally, alkaline stacks tend to be larger. Acta, later rebranded as Enapter has German-Italian origins but began collaborating with China in 2023. While this partnership has strengthened financial liquidity, it has also introduced logistical challenges, affecting transport routes and environmental conditions in production. As Enapter transitioned into an AG, administrative formalities have increased, leading to longer response times for customer inquiries. Despite occasional software issues, there have been no significant quality concerns. However, a key change in 2025 is that the Enapter electrolyzer will be sold without an integrated water treatment system. This change increases costs and requires additional research to determine the total investment. The 2022 price reference still included the water treatment system.
Model | Electrolyzer (EL 2.1), Dryer, Water tank, Water purification, Connectors, KOH Kit, Rack, Without Gas Tank |
H2 Flow Rate(NL/hr)/(kg/100km) | 501 |
Price € net | 25.625 € |
Price / Nl/hr €/W | 43,16 € |
In 2025, the EL 4.1 air-cooled electrolyzer will be available in a 35-bar version without water treatment for €17,745.00 net. This includes gas drying, a water tank, and some fittings.
Hydrogen Compressor Solutions: Performance and Maintenance Considerations
Sera, a German compressor manufacturer based in Hessen, produces a 2 m³/hr hydrogen compressor used in the PICEA hydrogen system. While the compressor offers reliable performance, a key concern is the cost and frequency of seal replacements, which the manufacturer has not yet specified. Understanding these maintenance aspects is crucial for long-term operational efficiency and cost management.
Model | pi-7007_02_de_agility_capability |
H2 Flow Rate (NL/hr)/(kg/100km) | 2000 |
Price € net | 26.000 € |
Price / Nl/hr €/W | 13,00 € |
Industrial Hydrogen Cylinders: Storage Capacity and Investment
A 16*50-liter bundle can store 240 standard cubic meters (Nm³) of hydrogen. To fill one bundle containing 493 kWh, the electrolyzer must operate for 480 hours. Achieving a hydrogen gas production target of 3,500 kWh would require seven bundles, leading to an estimated investment of €70,000. This setup ensures the year-round operation of a fuel cell forklift. During summer, electrolysis runs at full capacity to produce hydrogen, while in winter, the generated electricity is primarily used for direct consumption rather than storage.
300 bar 1 mano 1 section 1 ventil cylinders.cz | |
H2 Flow Rate (NL/hr)/(kg/100km) | 800 |
Price Neto | 12800 |
€/kWh | 34 |
Results and Insights: Electrolyzer Utilization and Hydrogen Production Efficiency
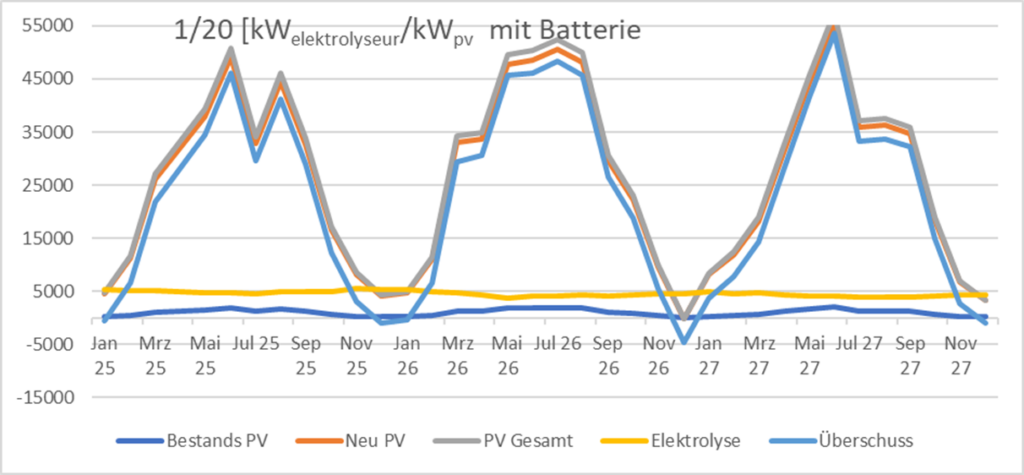
Illustration 4 Diagram of the PV surplus balance for PV systems larger than 30 kW peak with low capital for electrolysis
The electrolysis system can operate at full load for 10 months, contributing positively to amortization.
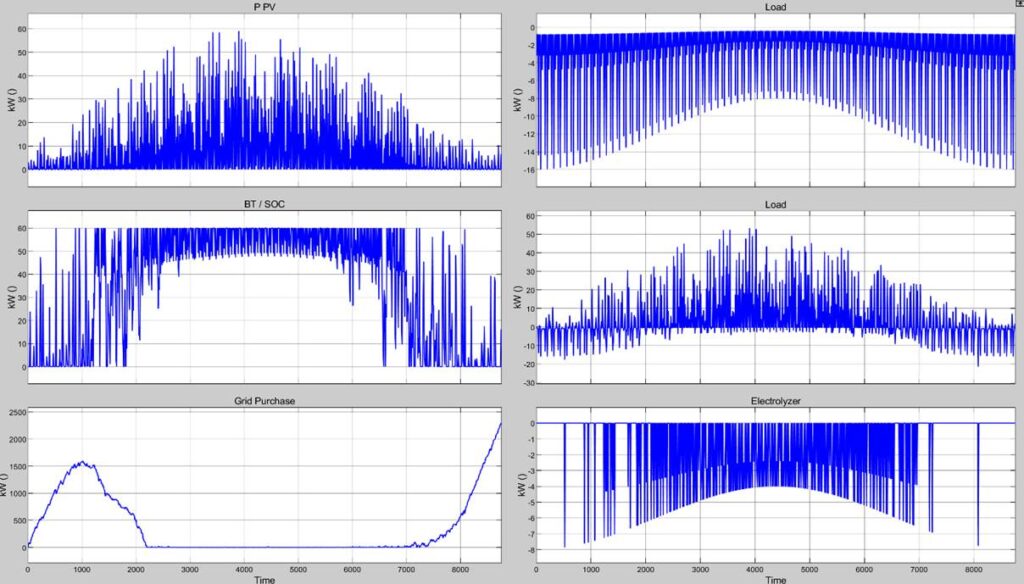
Figure Electrolyzer or dynamic load simulation on an hourly basis
The graphs illustrate the electrolyzer’s switching cycle over the 8,760 hours of the year. It functions only when the battery is fully charged and solar power surpasses electricity demand. In winter, additional power is needed to heat the water, and no hydrogen production occurs. The photovoltaic output is displayed in the upper left, while the middle left graph tracks battery charge levels. Electricity purchases are shown at the bottom left, and the middle right graph represents the house’s load curve with electrolysis. Internal electricity usage and battery status are also visualized.
An hourly analysis of power balance highlights that monthly evaluations are insufficient for accurately determining electrolyzer utilization and photovoltaic system efficiency.
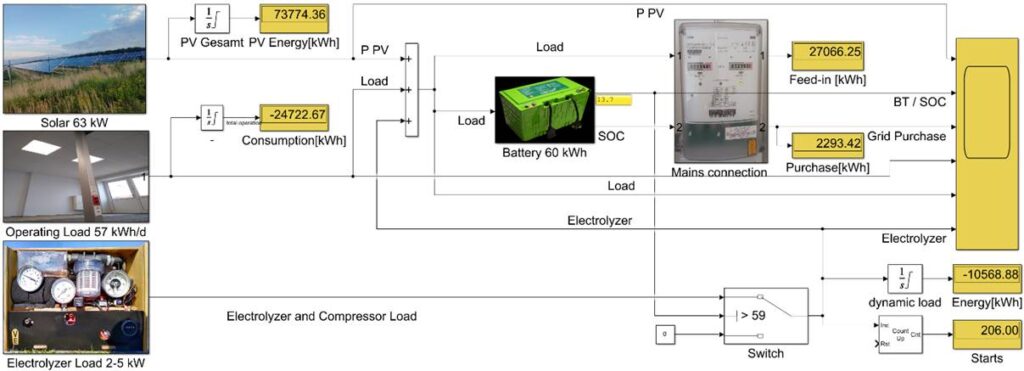
Figure Current account of green hydrogen production
Producing hydrogen with a 60 kW peak load presents challenges for both electrolysis capacity and gas storage. However, integrating a lithium battery allows a 2.5 kW electrolyzer to operate efficiently. The electrolyzer shuts down only in December and January, leaving 490 kWh of stored hydrogen.
A key limitation is that despite battery and electrolysis use, nearly 50% of converted PV electricity remains unused. To improve efficiency, direct marketing is recommended, especially for peak-period purchases.
The estimated cost for a 2.5 kW AEM electrolyzer, including a compressor, low-pressure gas tank, and 7,300 bar hydrogen cylinder bundles, is €159,700. Costs related to hydrogen utilization, such as for a fuel cell forklift, are not included.
Hydrogen Forklifts: Efficient Energy Solutions for Industrial Applications
The existing gas forklift currently consumes an 11 kg propane gas cylinder per week at about €31. With a calorific value of 12.87 kWh/kg for piston engines, the energetic value of propane gas in cylinders is therefore 22 cents/kWh.
The existing Jungheinrich TFG 16 forklift truck (1991-1997) has an output of 39 kW.
The efficiency of a liquefied gas forklift is estimated at 35%.
A hydrogen fuel-cell industrial truck can achieve an efficiency of 45%. This means that only 127 kWh of hydrogen would be needed per week, down from the previous 141 kWh with the propane forklift. Approximately 6,000 kWh are currently required for the gas forklift per year. Additionally, there would be no need to replace cylinders at the gas trader due to the self-produced hydrogen from electrolysis, giving it an equivalent value of 24.2 cents/kWh.
The fuel cell forklift may need to be refueled every 6-8 hours. This highlights that the strength of fuel cell forklifts only becomes apparent in shift operation. At this logistics company, a battery forklift could be charged overnight and would last a shift.
Ideally, the forklift’s fuel cell could provide base load electricity for the property overnight. However, such bidirectional hydrogen systems are not currently available from providers like Plug Power.
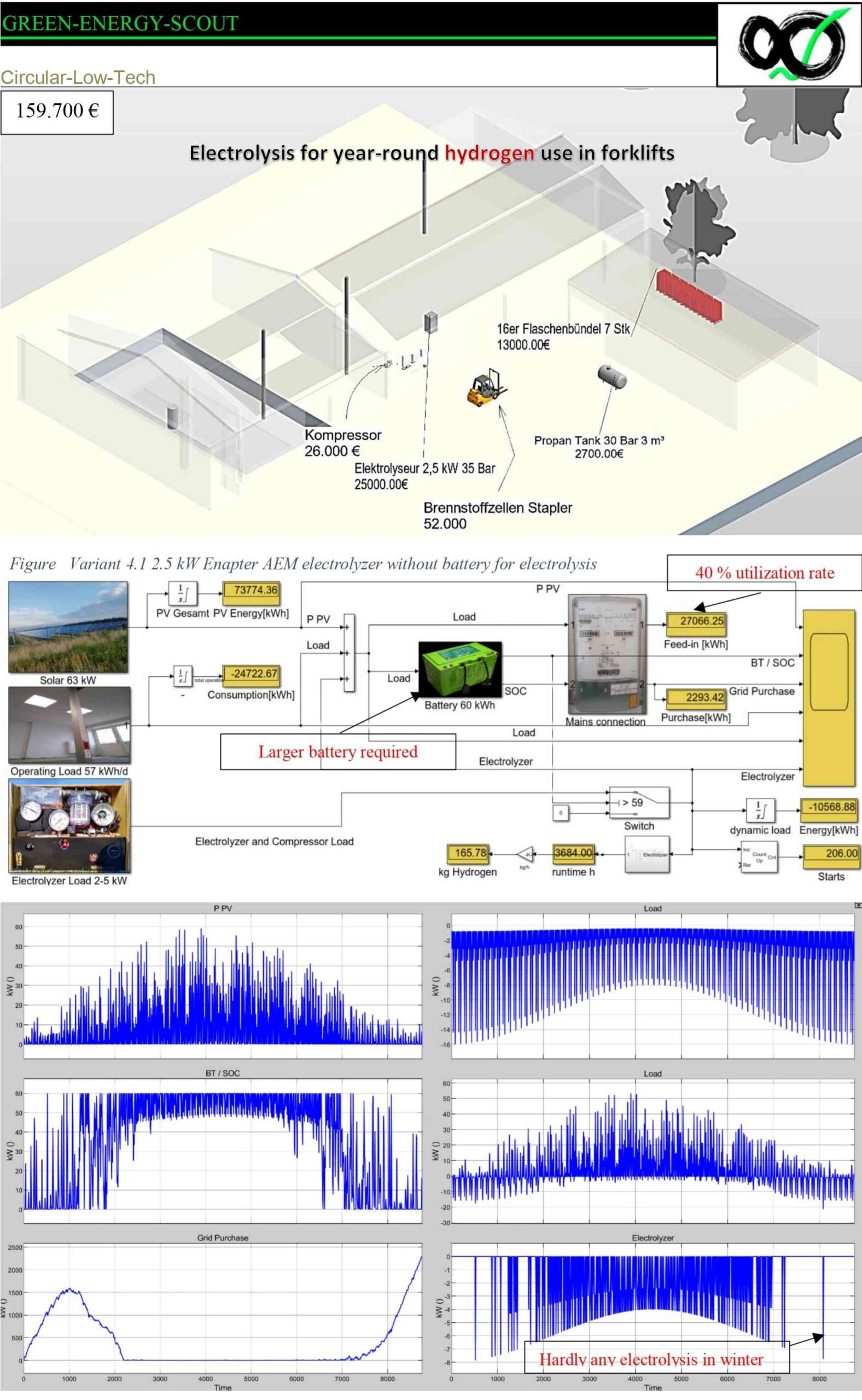
Conclusion for best Hydrogen Production Solutions
This study highlights the potential of combining a 2.4 kW electrolyzer with photovoltaic (PV) systems and lithium battery storage to create an efficient, decentralized hydrogen production system. By using detailed PV forecasts and hourly load profiles, the system is optimized for both residential and light industrial use. While the integration of electrolyzers and batteries significantly reduces energy curtailment and improves self-consumption, nearly 50% of PV electricity still goes unused indicating the need for additional strategies like direct energy marketing to enhance efficiency.
Technological comparisons between PEM, alkaline, and AEM electrolyzers, along with various battery storage solutions, reveal key performance, cost, and operational considerations. Enapter’s electrolyzers remain viable despite recent changes such as the removal of integrated water treatment, which increases complexity and overall investment. Lithium battery systems, while crucial for stabilizing hydrogen production and meeting peak demand, vary widely in cost depending on capacity. Choosing the right combination of components is essential for achieving optimal performance and economic balance.
The study also emphasizes the practical value of hydrogen for industrial applications, such as replacing propane-powered forklifts with fuel-cell alternatives. These offer higher efficiency and operational cost savings, particularly in multi-shift environments. Although current limitations—such as the unavailability of bidirectional hydrogen systems—restrict full flexibility, the overall findings support hydrogen as a clean and effective energy carrier. With thoughtful system design and strategic planning, integrated hydrogen-PV-battery systems can significantly reduce grid reliance and move closer to year-round energy independence.